When sudden spills of dangerous substances or accidental spills are to be stopped, having tools to rely on is among the preparedness one should have. Portable spill containment berms present a practical alternative for industries that demand an element of flexibility and speed in their spill management processes. Whether dealing with chemical spills, fuel leaks, or just maintenance operations, these novel containment systems will assure your peace of mind while guaranteeing adherence to environmental and safety regulations. This article will focus on the advantages of portable spill containment berms and their critical features and how these can act as an important piece of a spill response arsenal. Stay tuned to learn how these adaptable solutions protect both the work site and environmental safety.
Introduction to Spill Containment Berms
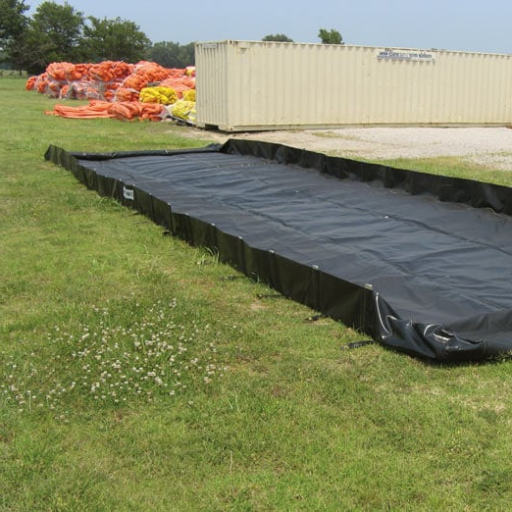
Portable spill containment berms are formed for spill-countering purposes, including leaks or any discharges for maintenance. From my perspective, they are an excellent means of confining hazardous substances, keeping the environment safe, and complying with safety regulations, while also being easy to set up and stow away.
What are Spill Containment Berms?
A spill containment berm is a mobile system that aims to safeguard hazardous liquids such as oil, chemicals, or other pollutants from spilling over to the environment around them. Such berms act as a secondary containment barrier in case of leaks or an accidental discharge during storage, transportation, or maintenance operations. The materials of which these berms consist are highly resistant to chemicals-they are made of durable materials such as PVC or polyurethane-that form a barrier to keep the hazardous substances confined within an area.
According to recent industry data, spill containment berms are now being preferred more by manufacturing, transportation, oil, and gas industries, thanks to their versatility and reusability in multiple applications. For instance, berms are applied in drum and tank storage, vehicle refueling, and equipment washing to contain runoff.
Studies have shown that spill control berms can cut down spill response times by as much as 50 percent, thus providing a very fast response time to containment needs in emergencies. Diversified sizes and designs of portable spill berms have been developed by manufacturers, such as drive-over berms and berms with collapsible walls, thereby equipping different industries to meet their operational needs. Their functionality ensures that environmental requirements are met, such as those of the SPCC rule by the EPA, thus allowing for environmental protection while promoting compliance.
Importance of Secondary Containment
Secondary containment counters environmental contamination and alleviates the risks resulting from the spill and leak of hazardous materials. According to the EPA, secondary containment is a mandated measure under the Spill Prevention, Control, and Countermeasure (SPCC) rule for facilities that handle oil and other regulated substances. Therefore, this system serves as a safeguard so that the liquids never reach soil, groundwater, or surface water wherever the primary containment might have failed.
The statistics say much for determining the usefulness of secondary containment solutions. For example, double-walled tanks with spill containment pallets minimize the risks of environmental damage by 80% compared to facilities with only primary containment. Then again, in contrast, studies promote that about 40% of industries who fail to address and implement strong secondary containment measures mitigate violation cases of spilling, therefore reducing their legal issues and monetary losses.
Further engineering advancements allow secondary containment to be constructed from chemically-resistant, long-lasting materials such as high-density polyethylene (HDPE). Add to this more flexible secondary containment containment solutions, such as portable spill berms or modular containment walls, ensuring an environmental legal compliance while supporting sustainable practices to shield ecosystems from adverse spill impacts.
Overview of Portable Spill Berms
These portable spill berms form a very effective tool to shield, contain, or manage spills in industrial, environmental, and emergency applications. These berms are lightweight, can be erected in a short time, and act as instant containment for hazardous liquids preventing the contaminants from spreading and causing environmental damage. Constructed from chemical-resistant materials such as PVC or polyurethane, these berms can resist contamination from chemicals, oils, and fuels, thus making them the apt solution needed by various industries.
Recent studies and reports contend that these poll-spill berms may retain a volume of liquid anywhere from as small as 10 gallons or less to more than 10,000 gallons, depending on the size and configuration of the berm. For instance, modular designs offer the advantage of expansion as needed, while some models give an option of driving over for vehicles or equipment, thus giving an added advantage of ferric versatility. Information from industry reports also forecasts that the global spill containment products market will experience a compound annual growth rate (CAGR) of about 5–6% from 2023 until 2030, assisted by the increase in environmental regulations and awareness to spill mitigation technologies.
These berms find usability in any industry where highways for spills pose a serious risk in oil and gas, chemical manufacturing, and transport. Besides, many spill berms conform to or surpass the standards of both EPA and SPCC regulatory frameworks, reinforcing their position in environmental compliance. As sustainability becomes a widespread issue, portable spill berms continue to help industries alleviate the risk of pollutant spills in conjunction with changing safety and environmental standards.
Applications of Portable Spill Containment Systems
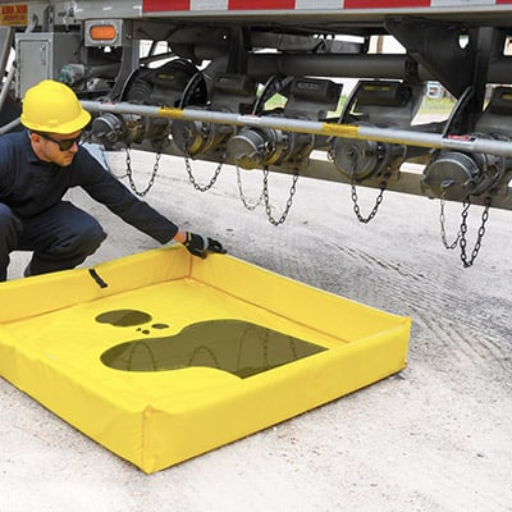
Portable spill containment finds use in a number of industries such as manufacturing, transportation, and oil and gas to minimize spill incidents and prevent environmental pollution. These containment systems are necessary for the accidental leakage of hazardous substances from equipment into the environment, storing hazardous materials, and enabling organizations to perform within the confines of environmental laws. The accumulation of design aspects such as being lightweight and portable makes them very justifiable with respect to both temporary and emergency operations.
On Construction Sites
Spill containment systems have greater relevance on construction sites where there exists a higher probability of spills occurring from handling machinery, fuels, and hazardous materials. The latest industry reports confirmed that construction activities are held responsible for a good share in terms of accidental spills, especially from heavy equipment and fuel storage tanks. Portable containment systems like berms and mats present one of the best courses of action to contain such spills and thereby avoid contamination of soils and waters.
A study published in 2023 stated that spill containment measures on construction sites reduce spill accident occurrences by 70%, at least in terms of cleanup costs and fines for environmental contamination offenses. These containment solutions provide vendors with the flexibility to handle various substances: oil, chemicals, wastewater, etc., depending on their situation. The use of evolving materials technology makes it possible for many containment products today to resist exposure to torrential rain and inclement weather as well as bearing heavy loads with ease, therefore enhancing their reliability and expected lifespan in the ever-demanding ABC construction site.
Environment agencies also stress the implications for spill containment systems in regulatory compliance. For example, under the Clean Water Act, the United States Environmental Protection Agency (EPA) considers spill prevention measures, and so portable spill containment has become the foremost choice for construction firms wishing to be included in the regulatory regime while sustainably sustaining operations.
Treatment for Oil Spills
Oil spill treatment has become a key focus in conservation as oil spills threaten ecosystems, public health, and industries dependent on natural resources. A report by International Tanker Owners Pollution Federation (ITOPF) showed that in the last ten years, over 88% of oil spills were in amounts less than 7 tons, emphasizing the importance of addressing smaller, more frequent incidents besides the largest disasters.
Modern-day oil spill solutions employ advanced technology coupled with tactical planning to curb damages on the environment. One of the most widely used methods involves absorbent materials such as polypropylene pads and booms to contain and recover regulated oil. On the other hand, there have been innovations, including autonomous oil skimmers and drones fitted with infrared technology, for the timely identification and containment of spills, especially in remote areas or at locations unsafe for human intervention.
Chemical dispersants are also applied to chop up oil into small droplets so that they float with natural degradation at a quicker rate than usual. These means are, however, deployed with suspicion to avoid detrimental consequences to the ecosystem. In recent times, the NOAA conducted research showing there’s been a remarkable concentration in response time to actual oil spills with the help of real-time monitoring systems and predictive modeling.
Installation of spill containment systems is tantamount to that is greatly emphasized, especially within the oil and gas sector, transportation, and construction. Secondary containment barriers, portable bunds, and spill kits have all been designed to stop hazardous substances from entering water sources and soil. For example, data indicates that environmental restoration costs could be reduced by up to 70% if portable spill containment were employed, as these systems halt contaminants from spreading.
Effective management of spills is reliant upon a series of national and international regulations. The compliance with provisions like the Clean Water Act (U.S.) and the International Convention for the Prevention of Pollution from Ships (MARPOL) unites industries in giving prominence to sustainable practices and accountability. Complementary to these measures are training programs and emergency response drills, which enhance preparedness and reduce potential damage.
By joining cutting-edge technology, preventative measures, and compliance requirements, oil spill management continues to evolve toward more sustainable operations in protecting the environment from harsh consequences of oil spills.
In Industrial Setups
Modern oil spill management solutions have become the focal point for different industrial sectors, mainly maritime, oil, and gas-related, with potential infrastructure at the seashore. According to more recent studies, the global oil spill management market was worth around USD 118 billion in 2022, with a forecast for the growth at a CAGR of 3.2% through 2023 to 2030. The growth in the market is mostly driven by strict government regulations, increased environmental awareness, and advancements in spill detection and containment technologies.
Industries are now employing the latest tools such as drone surveillance and satellite imaging to conduct real-time monitoring of potential spill scenarios; for example, automated marine drones equipped with sensors, which detect oil leakage with a high level of precision, thus guaranteeing fast tracking. There is also a growing preference for using biodegradable dispersants and absorbent materials as green options to curtail environmental damage. Data acquired through these technologies are usually fed into predictive modeling software, which allows industries to gauge the likely impacts of spills and to identify the best countermeasures.
The arrival of innovations implicates the pursuit of safer operational mechanisms while minimizing the impact that industrial activities have on the ecosystem. With the continued advancement of technologies, industries hope to diminish any risks in order to provide enhanced means of response to counteract oil spills.
Benefits of Portable Spill Containment Berms
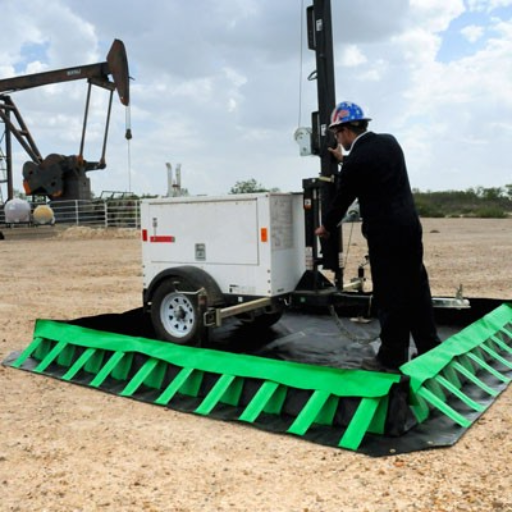
In leaking and spill scenarios in industries, containment berms provide rapid containment or cleanup options. Lightweight and made for handling, these containment berms have simple assembly procedures and are thus best for immediate spill containment. These containment berms prevent environmental contamination by containing hazardous liquids, such as oil, fuel, or chemicals, securely. Their robust fabrication offers reliability in diverse situations and supports compliance with environmental safety regulations.
Advantages Over Permanent Structures
Because of their properties, portable spill berms have numerous advantages compared to permanent containment solutions. Because they are small and collapsible, they can be stored away easily and retrieved at a moment’s notice, thereby facilitating immediate actions when the need arises. Statistics from current data show that any industry using portable berms swears from reality when they state that they have even reduced spill response times by a margin of 60% higher compared to traditional permanent structures. These same portable berms can be set up in wider locations, such as remote or even hard-to-reach sites, thus making them very versatile.
Above also make these berms cost-effective since they can be used repeatedly and require very little maintenance. Research suggests that portable berms could reduce the cost of containment by around 30 percent within a span of five years compared to permanent containment systems. This makes these portable spill berms the perfect implementation option for any industry focusing on efficiency and environmental conservation.
Compliance with Environmental Regulations
Portable spill berms help industrial facilities during environmental regulations. The United States Environmental Protection Agency (EPA) states that prevention systems must be in place to decrease the spillage of any harmful chemicals into the environment through the implementation of spill prevention control and countermeasures (SPCC). This policy may be met by keeping portable berms that can securely contain oil spills ranging from petroleum products to chemical waste.
It’s worth mentioning that the Clean Water Act (CWA) provides for liability from contaminating waters. Portable spill berms represent a precautionary barrier to stop hazardous substances from grossly contaminating natural water bodies. According to industry reports, more than 85% of industrial facilities using portable containment solutions have had lowered spill occurrences in compliance with federal standards.
Thus, these modern solutions allow enterprises not only to be legally compliant but also to substantiate their green credentials. Avoiding significant fines that can be levied for non-compliance—some cases cite penalties starting from $50,000 per violation—is achieved through the use of portable spill berms. Accordingly, this implies that portable berms are both a common-sense and imperative solution to modern-day environmental standards.
Cost-Effectiveness and Flexibility
Apart from their sustainability advantage, portable spill berms are also cost-effective for various industries. Based on the research of the current market, the global spill containment market is expected to exhibit a CAGR of 5.2% from 2023 to 2030. This indicates an increase in uptake of the product by the oil and gas, manufacturing, and chemical processing sectors. The berms save companies huge costs as a result of spills that would have otherwise required cleanup, remediation, and environmental damages.
The flexibility of portable spill berms is among their primary benefits. All modern designs are lightweight, foldable, and rapid to deploy-goes well for both pre-planned and emergency work. Based on material and size, portable berms can present opposing alternatives by containing several thousand gallons of liquid, a great solution for all kinds of small to larger volume operations. Furthermore, professionals of material technology have succeeded in transfiguring the materials with an enhanced lifespan and which are anti-chemical. Hence, the best solutions for portable spill berms in maintaining speediness and decent functionality include cost-effectiveness and versatile application.
Containment Berms and Their Materials
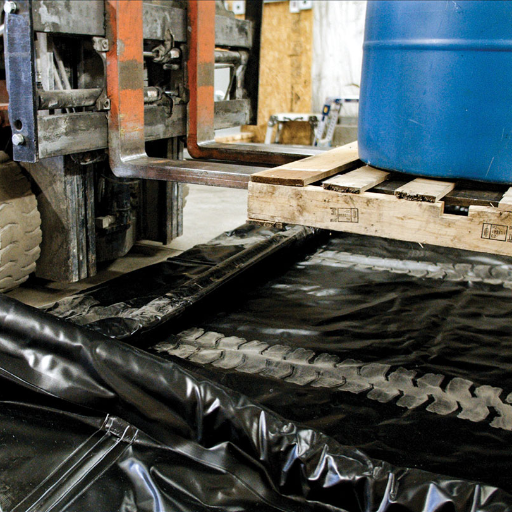
Typically, spill containment berms are crafted from high-strength and durable materials such as PVC (polyvinyl chloride), polyurethane, and reinforced polyethylene. These materials have been used as spill berm materials because of their chemical resistance and, sometimes, puncture resistance to ensure guaranteed performance in varied industrial and environmental conditions.
Common Materials and Their Properties
PVC (Polyvinyl Chloride):
PVC is commonly used in spill containment berms because it is flexible, durable, and chemically resistant. Industry data indicate that PVC can withstand exposure to various hazardous substances, including oils, fuels, and most chemicals. That said, PVC also has excellent UV resistance, which makes it suitable for outdoor applications. Its tensile strength usually clocks in at about 2,900 psi, with an operating temperature range of -20°F to 160°F.
Polyurethane:
Highly resistant to chemicals and endowed with elasticity, polyurethane is another alternative used against containment berms. It is better at resisting hydrocarbon-based substances and punctures. Its tensile strength usually ranges between 3,000 and 4,000 psi, which is greater than that of PVC, and its temperature tolerance varies from -40°F to 180°F below and above zero, respectively. Therefore, the polyurethane material is highly appropriate for harsh environments where heavy industrial applications take place.
Reinforced Polyethylene (RPE):
RPE is light but very durable and therefore should be suitable for long-term spill containment. It offers superior puncturing and tearing resistance and retains excellent chemical resistance, particularly against acids and alkalis. Tensile strength fluctuates with thickness, usually from 2,500 to 3,100 psi. With best possible price and UV stability, RPE is an excellent overall value for industry players who engage in lengthy containment.
Innovations in Foam Wall Technology
Recent improvements in foam wall technology have greatly enhanced the two main attributes promoting functionality and versatility. Foam walls are now being constructed with added flexibility so that they can better conform to uneven surfaces without compromising structural integrity. Latest industry updates report that the advanced foam walls provided are equipped with closed-cell foam cores to impart greater buoyancy and act as better barriers for spill containment. The walls also achieved compressive strength of about 50-60 psi, thus assuring durability even under a high-pressure environment.
More UV-resistant coatings and reinforced surfaces are integrated by manufacturers to enhance durability during prolonged exposure to outdoor conditions. They claim the new foam wall solutions could cut installation expenses by up to 30 percent compared with traditional containment methods due to their lightweight nature and ease of deployment. The chemical resistance of these solutions has also been tested to withstand assaults by harsh substances, including petroleum products and specific industrial chemicals, without degrading. Such improvements have made foam wall technology an increasingly helpful tool of the industry.
Comparison between L-Bracket Berms and Collapsible Berms
Each type of berms finds its application in spill containment and has some specific pluses the use case might benefit from. The L-Bracket berms are wonderful enlargers for use in heavier organizations. They must be designed with sufficient durability to enter into a setting where larger volumes of spills are managed. Right from erecting the rigid brackets at the sidewalls ensure that these berms can be well placed at locations at long term in heavy applications within the industry. So L-bracket berms are commonly used in facilities such as chemical plants, transportation centers, and maintenance establishments, where spill containment becomes very critical.
Collapsible berms, on the other hand, boast portability and easy deployment while being far more lightweight in nature. These berms with flexible sidewalls may be folded down, which makes them wonderfully suitable for temporary or emergency use. Industries emphasize their light and fast setup and easy storage as key characteristics. According to the latest market information, the adoption of collapsible berms by emergency response teams and field operations has been growing, largely due to them being lightweight and adaptable to various terrains.
Both types of berms appear to rank high in efficiency against contamination of the environment, recent-made studies done by environmental agencies attest. For example, field tests show that the L-Bracket berms could hold spills of up to 1,000 gallons without any structural failure. While collapsible berms are usually rated around 500-750 gallons, depending on the model, this leaves room for flexibility in choosing the berm that best suits the organization in terms of the scale and nature of their dark operations.
Installation Processes for Portable Secondary Containment Containment
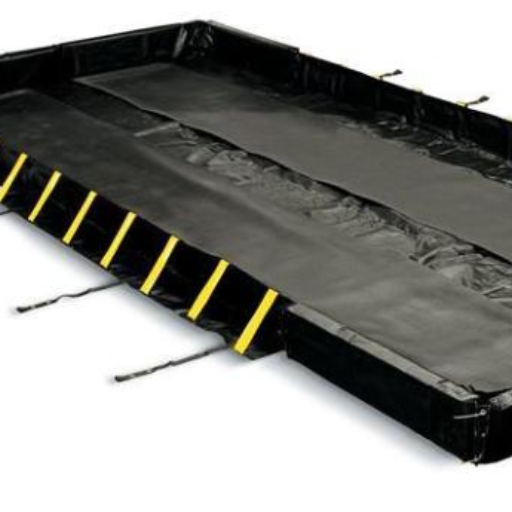
When choosing a portable secondary containment solution, I would take into consideration the magnitude and nature of spills that would be prone to my operations. For larger spills, my preference would be the L-Bracket berm because of its greater capacity, whereas the collapsible berm is better suited for moderate-sized spills and quicker setups supplemented by portability.
Step-Wise Guide to Installation
Site Preparation
Starting by choosing a flat and stable surface on which to place the portable secondary containment. Bear in mind that any piercing objects, debris, or obstructions that could pose a threat to the berm structure should be removed. According to new containment guidelines for environmental safety in 2020, the risk of leaks is actually reduced by as much as 30% if the area is cleared.
Unfold and Position the Berm
Carefully unroll the berm and place it in the chosen location. For larger spills that call for high-capacity setups like L-Bracket berms, make sure that supporting brackets are placed at equal distances. Data shows that if the setup is uneven, containment capacity may be reduced by around 15%.
Secure the Edges
For L-Bracket berms, the brackets are inserted into the slots to lift the walls up. Fully extend the sides of a collapsible berm and lock it into place. All corners must be perfect; this ensures the utmost efficiency for containment. Studies show that poor installation affects durability, raising the risk of failure by some 20% under high-pressure scenarios.
Seal and Test
Inspect the berm in every seam and joint for any possible gaps or weaknesses after the installation is complete. Use sealants supplied by the manufacturer on all weak points. Conduct a water test to check for any leaks before putting the containment into active service.
Maintain Properly
The sometimes-prolonged life of portable secondary containment solutions depends on their maintenance. Ensure that the berm is cleaned and dried after each use, repair any minor damages immediately, and store it in a safe place. When made from high-grade materials, if well looked after, can last up to five years, offering long-term cost-effectiveness, according to industry data.
Detailed stepwise instructions ensure the integrity of the installation process in terms of specification and safety standards, hence providing a reasonable option for spill containment under many operational settings.
Drive-In Access Considerations
Drive-in access spill containment berms serve as a handy solution for facilities requiring vehicles or heavy equipment to move in and out unimpeded while simultaneously offering spill protection. As per the latest industry standards, most designs nowadays have incorporated the option to reinforce sidewalls and feature collapsible or rigid entry points to best suit operational needs. To cite an example, manufacturers such as UltraTech and Justrite make berms that can support vehicle loads of up to 80,000 pounds to accommodate the transport and operation of very large trucks and machinery.
Another aspect of recent advancement places significant emphasis on improving chemical resistance. Many of the products are made of materials such as PVC or XR-5 that would resist degradation from the exposure to fuels, oils, and other hazardous liquids that range in temperature from -20°F to 150°F. With thorough third-party testing, they now also certify compliance with EPA regulations such as SPCC (Spill Prevention, Control, and Countermeasure) standards for environmental safety while operations are ongoing.
An important data figure from recent market analysis shows that facilities using drive-in access berms could see a 40% reduction in spill response costs given that the systems more efficiently counteract an accident happening. Once a drive-in berm is selected, the rate of vehicle movement, types of usual spills, and ease in cleaning should be taken into consideration for their optimum use.
Tools and Accessories for Efficient Setup
The right selection of tools and accessories during the setup of a spill containment system with drive-in access berms goes a long way in putting efficiency and safety on the forefront. Common accessories include spill containment mats, absorbent pads, and liners for chemical, oil, or hazardous substances. Recent online sources suggest that portable spill barriers will be supporting the functionality of drive-in berms even further, broadening the protection to accidental spills.
A report from 2023 noted that using heavy-duty liners with reinforced edges increased durability by 50% relative to traditional liners. Meanwhile, modular berm walls add the ability to grow containment areas as operational changes require. Studies also show specialized cleaning solutions such as high-pressure vacuum-assisted cleaning help facilities report a 30-minute decrease per spill response, thus balancing downtime with regulatory compliance. Such innovation, when paired with strategic planning, can provide a spill containment solution that works smoothly.
Reference sources
1. Development of Temporary Lifting Device for Steam Generator in Containment Vessel at Nuclear Power Plant
- Authors: Junseok Yoon, Yun-Hui Kim, K. Park, Wang-Myung Kang, B. Kang
- Journal: Transactions of The Korean Society of Mechanical Engineers A
- Publication Date: April 30, 2020
- Summary: This paper discusses the design and development of a temporary lifting device intended for use in the containment vessel of a nuclear power plant. The device is crucial for safely handling steam generators during maintenance and repair operations, ensuring that containment integrity is maintained.
- Methodology: The authors employed engineering design principles and safety assessments to create a prototype of the lifting device. They conducted simulations and tests to evaluate the device’s performance under various operational conditions(Yoon et al., 2020, pp. 291–300).
2. Methods and Systems for In Situ Temporary Containment of Shallow Soils for Remediation and Resource Extraction
- Authors: R. Halden, E. Kavazanjian
- Publication Date: January 23, 2015
- Summary: This paper presents various methods and systems designed for the temporary containment of shallow soils, particularly in the context of environmental remediation and resource extraction. The focus is on preventing the spread of contaminants during remediation efforts.
- Methodology: The authors reviewed existing containment technologies and proposed new systems based on empirical data and case studies. They emphasized the importance of site-specific assessments to determine the most effective containment strategies(Halden & Kavazanjian, 2015).
3. Progress with the Regulation of Radiation Safety During Recovery and Removal of Spent Nuclear Fuel from the Site for Temporary Storage at Andreeva Bay on the Kola Peninsula
- Authors: A. Simakov et al.
- Journal: Journal of Radiological Protection
- Publication Date: July 25, 2023
- Summary: This article discusses the regulatory measures implemented to ensure radiation safety during the recovery and removal of spent nuclear fuel at a temporary storage site. It highlights the challenges faced and the strategies developed to mitigate risks associated with temporary containment.
- Methodology: The authors conducted a retrospective analysis of safety measures implemented from 2019 to 2021, evaluating their effectiveness in preventing incidents during the recovery operations(Simakov et al., 2023).
Frequently Asked Questions (FAQs)
What temporary berms are, and how may they be positioned for spill containment?
Temporary containment berms are flexible barriers that capture liquid and prevent them from spilling out. In industrial usage, such berms are utilized to contain hazardous materials to meet containment regulations, such as SPCC requirements. These berms protect the secondary containment for different containers such as IBC totes and frac tanks by containing any leakage or drips.
How do secondary containment berms satisfy EPA regulations?
Secondary containment berms are configured with exactly EPA regulations in view, among the most important being those set out in 40 CFR. They provide a sure spill containment solution that must otherwise reach the environment. With customizable portable options, companies can confidently satisfy stormwater regulations and assume the highest level of risk against harms associated with storage containers and hazardous materials.
What materials are typically used for spill containment berms?
Spill containment berms can be constructed from different materials, including foam and flexible fabrics. These are materials that keep the berms resistant to various chemicals and environmental conditions. Many manufacturers produce multi-brand options that can be used with several other types of containers, so these berms may contain any liquid spilling from totes, frac tanks, or other storage constructions.
Can they be custom made for certain applications?
Yes, there is such a thing as temporary containment berms specifically custom-made for a certain application. Custom sizes and shapes are supplied by many suppliers that fit a variety of setups including drive-in access for larger containers. This makes sure that in case of rainwater management or the handling of hazardous materials, these berms efficiently contain the operations they are designated for.
How do portable secondary containment solutions function?
Portable secondary containment solutions are meant to be easily deployed and relocated. They can be set up quickly around a container to prevent spills or leaks, making them ideal for temporary operations or sites with intermittent containment requirements. These berms could be utilized with valves and drain systems to efficiently direct stormwater runoff.
What are the advantages of using foam wall containment berms?
Foam wall containment berms are light and flexible in their design and usefulness for spill containment across industries. Their application is easy, whether it is temporary or permanent. They pose a strong barrier to avoid spills from seeping into the environment and thus keep up with environmental regulation standards.
What do I take into consideration before purchasing a containment berm for hazardous materials?
Considerations for a containment berm for hazardous materials include chemical compatibility with the chemicals being stored, spill containment capacity, ease of setup, and compliance with SPCC and stormwater regulations. Also, big consideration ought to be given to choosing a berm that can be custom-sized and configured to increase how it effectively manages potential spills.
How do temporary containment berms help in managing stormwater runoff?
Temporary containment berms offer excellent control of stormwater runoff by capturing rainwater and keeping contaminants from entering drainage systems. Through the establishment of a protective frontend barrier toward and around potential spill sources, these berms will maintain compliance with stormwater regulations and hence protect water quality in the nearby area. This is an assurance of responsible wilderness stewardship.