Choosing the right materials can greatly affect your home’s protection against the elements. For many years, housewrap has been considered the traditional method of weatherproofing a house beneath exterior siding. In these recent years, the synthetic roof underlayment has entered the discussion, suggesting one possible alternative and questioning whether it can be used in place of the housewrap. Is it a good opportunity, or does it have its hidden drawbacks? Our blog post considers the pluses and minuses and important considerations about synthetic roof underlayment as housewrap to guide your decisions in favor of your home.
Defining Key Terms
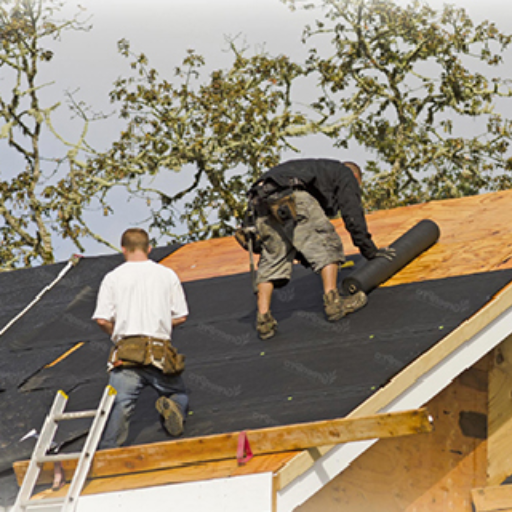
What is Synthetic Roof Underlayment?
Synthetic roof underlayment is a contemporary roofing material designed to act as a waterproof barrier between the roof cover (shingles) and the roof deck. Contrary to traditional felt underlayment fashioned from asphalt-impregnated paper, synthetic roof underlayment comprises durable polymers, such as polypropylene or polyethylene. This superior composition makes it weather-resistant against moisture, tearing, and UV rays, rendering it a highly versatile option for both residential and commercial applications.
This underlayment is increasingly being adopted by the construction industry in recent years due to its enhanced performance. According to market research reports, the global synthetic roofing underlayment market was pegged at approximately fifteen hundred million of dollars in 2022 and is projected to witness a CAGR of 5.2% till 2030, fuelling demand for more robust, lightweight, and long-lasting material for roofing systems. Also, some synthetic underlayments have anti-slip coatings, which enhance safety during installation as opposed to felt for the traditional variety.
The other distinguishing property is its resistance to water. It has been revealed in studies that synthetic underlayment can be subjected to an exposure of water and harsh weather conditions for a period ranging from weeks to even months without losing any integrity in its functions. This alone makes it an ideal candidate for construction in regions with heavy rainfall or storms. While synthetic underlayments are recommended for their durability, proper application procedures and compatibility should also be reviewed when substituting for housewrap, as their uses and features are not always exactly that of one another.
What Is House Wrap?
House wrap is primarily used as a synthetic material that protects buildings from moisture penetration while allowing vapor to escape. This barrier, known for breathable properties, is generally installed under siding for a house and is crucial for energy efficiency air infiltration control and mold or moisture-related problems.
Further enhancements establish the ever-growing use of house wraps in modern construction methods. Forecasted by market analysis, the house wrap industry shows expected growth at a CAGR of more than 6% between 2023 and 2030. In this field leading manufacturer DuPont Tyvek offers house wraps that maintain good durability and UV resistance and have been tested for exposure for up to four months without damage.
Studies confirm that house wraps save energy, with a good house wrap reducing heating and cooling costs by 15%, on average. Current variations of house wrap also have improved tear and puncture resistance, ensuring long-term protection in severe weather. These qualities make house wrap an essential construction material used in both residential and commercial projects.
Differences Between Synthetic Roof Underlayment and House Wrap
Although synthetic roof underlayments and house wrap serve the protection of an edifice against the elements, these two have separate sets of purposes and specifications. Synthetic roof underlayment is meant to create a waterproof barrier beneath roofing materials so that any leakage can be contained. Protection is offered from damage caused by rain, snow, and ice. Advanced synthetic underlayments now offer enhanced durability, resistance to high temperatures, and anti-slip properties, which provide a safer installation over traditional felt underlayment.
Conversely, house wrap acts as a breathable barrier to walls preventing air and water infiltration while allowing moisture vapor to escape. However, studies have shown house wrap to improve energy efficiency by 10-15% when properly installed as a result of reducing drafts and moisture management. Advanced high-performance house wraps provide much-extended resistance to UV degradation and tears while maintaining their functionality.
Price-wise, synthetic roof underlayment is generally priced at $0.15 to $0.50 per square foot depending upon thickness and brand. House wraps are commonly priced between $0.25 and $0.50 per square foot. Thus, both materials are cost-effective ways to enclose a building’s outer envelope for many years. The choice of which to use depends on the application and environmental concerns posed by a specific building.
Primary Functions of Synthetic Roof Underlayment and House Wrap
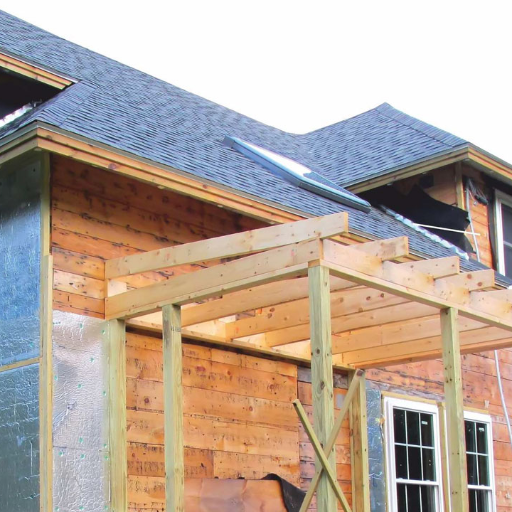
Both synthetic roof underlayments and house wraps direct their protective functions towards buildings. A synthetic roof underlayment is placed underneath roofing materials mostly for the added waterproofing effect synthesized from entry of water into the roofing structure. A house wrap is laid saunter beneath the siding as a moisture and air barrier to reduce energy consumption and to protect the structural members from water damage. Choice depends highly upon the part of the structure to be covered and the type of protection it must bestow on the project.
Roles of Synthetic Roof Underlayment in Roofing
With Synthetics: Synthetic roof underlayments mean modern roofing technologies long considered best in terms of protection would be upgraded over the traditional uses of asphalt felt, for instance. Made out of quite sturdy polymers, synthetic types of underlayment assist the roofing to be more resistant to water infiltration and wind-driven rain while still being very light in weight. Contrary to asphalt felt, which can absorb water and degrade over time, synthetic varieties are constructed-tobe waterproof-and capable-of retaining-their-integrity-for-extensive exposure to-the-elements.
Industry studies would demonstrate the synthetic underlayment to be at least 20 times stronger than traditional asphalt felt, which means it is able to hold out better during installation and for the duration of the roof’s life. It gives them very high resistance to tearing, even blowing in adverse weather conditions, thereby making them applicable in locations that receive high wind or heavy downpours. Synthetic materials are generally coated with UV-resistant for sustainability upon prolonged exposure to the sun.
Further, advanced technology has also made synthetic underlayment safer and easier to use. Many products offer slip-resistant surfaces that greatly enhance roofer traction, thereby avoiding injury. The incorporation of grids or patterns to assist in accurate cutting and alignment is a prime example of this type of technology.
Green matters should be brought to bear. Being lightweight improves the environmental attributes of synthetic roof underlayment by reducing transportation emissions, and some manufacturers go a step further and utilize recycled materials in the production of these underlayments, all in support of green construction.
In a nutshell, synthetic roof underlayment is one of the most important elements of a modern roof for protection over time, ease of installation, and performance enhancement in different conditions. Homeowners and contractors benefit from all of its advanced technology features, which help protect structures while improving the durability and reliableness of roofing systems.
Functions of House Wrap in Building Envelopes
An essential function of house wrap is to preserve the integrity of the building envelope as a barrier to external conditions. House wraps are designed to resist water penetration and keep liquids from the outside world from entering into the cavities of walls that could harbor mold, grow into structural damage, or deteriorate insulation performance. At the same time, they are vapor-permeable from inside, allowing trapped atmospheric moisture from within to escape with the help of house wrap for keeping a healthy indoor environment.
New statistics indicate increased use of house wrap in residential and commercial construction thanks to better energy efficiency. Energy conservation of up to 15% has been reported for buildings using house wrap with adequate insulation, according to industry statistics. This is mainly because the house wrap reduces air leakage, thereby less heat loss occurring inside during winter and retention of cooling hinting during summer. Most house wraps currently tested against ASTM standards for water resistivity and permeability ensure a good balance between durability and breathability.
These improvements have made house wraps one of the best cost solutions for protecting and enhancing building envelopes in various climates. For example, some wraps can remain useful for 9 months of UV exposure and give planners enough freedom in defining construction procedures without having to weigh the wraps’ degradation as a performance factor.
Sealing and Moisture Control
House wrap offers wonderful air sealing for energy-efficient construction, as well as for sustainable, durable building envelopes. It is built primarily to limit any infiltration or exfiltration of air that would otherwise lead to significant energy-wasting impacts. Different researches point out that air sealing through house wraps can reduce heating and cooling energy consumption by as much as 30%, symbols of sustainable building practice.
Choosing for moisture control, house wraps stop liquid water from entering and permit water vapor out. This facilitates lessening the risk of having good moisture conditions to create mold, mildew, and structural damage. With the highest permeability ratings, advanced wraps achieve basically above ten perms, giving some of the best products on the market. The wrap’s balance of water-shielding versus breathability makes it an ideal option for mixed-climate areas.
Industry data also indicates that properly installed and sealed house wrap application is considered to reduce moisture-related hazards, and in all possibilities, may increase the lifetime of siding and framing building materials. These developments are turning the house wrap into a necessary product for modern-day construction, ensuring energy efficiency and long-term durability.
Comparative Analysis
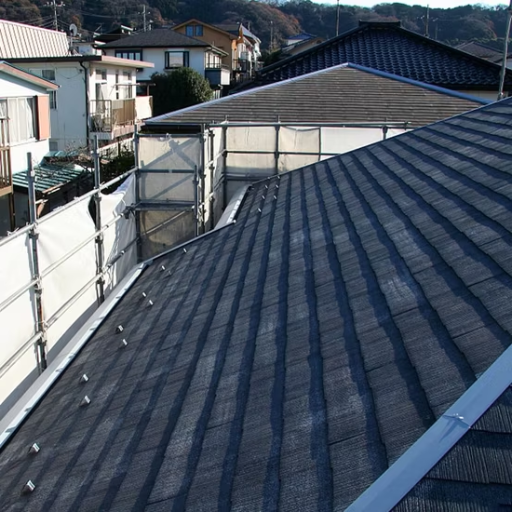
The house wrap offers a basic defense against moisture while helping the building breathe. It allows water to go inside, which may lead to moisture and rot, plus it improves the energy efficiency of a building by allowing fewer drafts inside. Correct installation and sealing must be guaranteed for the house wrap to provide maximum protection to the structure and materials in the guise of premature deterioration and damage. For these reasons, house wraps are an essentially today-used component in durable and efficient construction.
Advantages of Using Synthetic Roof Underlayment as House Wrap
There are several advantages posed by synthetic roof underlayment when applied as a house wrap, providing great durability and versatility. Unlike felt materials, synthetic underlay is generally made by weaving or spinning polypropylene, which imparts greater resistance to tearing, UV degradation, or moisture infiltration. It has been found through research that synthetic underlayment will in fact resist water better than the normal house wraps, with permeability ratings usually above 50 permsOne of the main qualities against protector, durable performance in difficult weather conditions.
They are lightweight and simple to install. Other features would include their ability to apply anti-slip characteristics to construction procedures for further safety and efficiency. These materials are tested against extremes with temperature variations all through freezing cold ones to intense heat without any converse application inefficiency. Recent market research highlights the growing preference for synthetic roof underlayment over traditional house wraps, projected at $40 billion worldwide by 2027, with an expected growth rate (compound annual) of 5.1% over that period.
The increased longevity and superior performance of synthetic materials mean they also promote energy efficiency in addition to moisture protection as a great air barrier. By reducing air infiltration, synthetic underlayment helps to maintain consistent indoor temperatures and reduces the load on HVAC systems, which in turn lowers energy costs. These compelling reasons make it worthy of consideration by any builder or homeowner seeking long-term protection of structures and sustainability in utilities.
Disadvantages and Limitations
While synthetic underlayment offers many benefits, it is not without its disadvantages and limitations. One of the primary concerns is its higher initial costs versus traditional asphalt felt. Updated industry data shows that synthetic underlayment ranges from 20 to 60 cents per square foot, while asphalt felt runs around 10 to 20 cents per square foot. This might make a significant difference in cost for those saving every penny for their project.
The other limitation relates to proper installation techniques. Poor installation practice reduces its effectiveness as an air and moisture barrier, which causes damages to the structure with time. Moreover, the product can be unsafe when it gets wet and slippery, potentially creating safety hazards for workers during its installation. Many manufacturers have developed textured and anti-slip performance surfaces in recent years to counteract those concerns, although the risk remains high when working on steep or complex roof designs.
From a sustainability standpoint, however, there is now considerable debate about disposal. While synthetic underlay provides enhanced longevity and energy efficiency, it is largely composed of non-biodegradable substances like polypropylene and polyethylene. Due to plastics ending up as the biggest contributors to solid wastes in general, there are considerable concerns as to how sustainable these will be in the future.
Builders and homeowners must take their disadvantages into consideration and measure them against the benefits to make sure synthetic underlayment is the right choice for their project and priorities.
Expert Views Regarding the Suitability of Synthetic Underlayment
In general, consultants of the roofing and construction industries accept synthetic underlayment as a top-quality product with distinct benefits over conventional felt underlayment. Through the research compiled by the National Roofing Contractors Association, it contends that synthetic underlayment has high durability, is resistant to tearing, and leakage of UV rays for long periods, thereby giving the contractor more options during roof installation projects. Synthetic underlayment is resistant to water and lacks resistance to mold, which underlies the structure with greater long-term protection.
Sustainability experts, however, deprecate the reliance on plastic chemicals such as polypropylene and polyethylene Said to these materials are not biodegradable, needing a classification of hundreds of ages before decomposing in landfill sites, as shown in research reports. While there may be an option to recycle these, the facilities to properly dispose of and recycle these plastics remain restricted in many regions.
When regarded from a performance perspective, aside from a recent 2023 market analysis report concerning synthetic underlayment, such materials continue 25 to 40 percent longer than does the normal felt. This increased performance ensures a major roof lifespan and thus less frequent replacements, thereby eventually leading to cost savings for homeowners. However, from an environmental point of view, alternatives or hybrid systems that combine sustainable components should be considered to reduce the environmental impact.
Overall, synthetic underlayment is regarded by many as a reliable and proven component for roofing. Builders are advised to consider the scope of the project with consideration of cost and environmental issues to decide whether there might be a place for this material in their goals. Additional advancements in recycling and biodegradable programs would help find a better answer between performance and sustainability).
Case studies and real-life applications
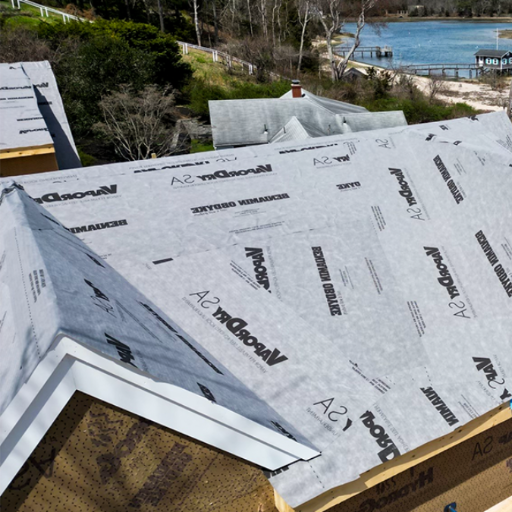
Synthetic underlayment is a reliable and efficient roofing option, I feel. However, it must always undergo consideration of the type of project in hand: budget, environmental factors, etc. Sustainable practices should lead the way; for instance, recyclable or biodegradable materials may need to strike a balance between performance and eco-friendliness.
Case Study Example: Successful Implementation of Synthetic Roof Underlayment
The newly introduced synthetic roof underlayment is a nerve to consider in greatly advancing the durability and functionality of the material with respect to its felt-based counterpart. According to an industry report, synthetic underlayment can last up to fourfold that of asphalt felt-doing so under ideal conditions for 20-30 years. Furthermore, most of the newer synthetic underlayments are designed so they never get affected by UV exposure, extreme temperature variance, or maybe water infiltration, thus guaranteeing long-term performance even in harsh climatic conditions.
In effect, the National Roofing Contractors Association (NRCA) highlighted in their 2022 study that homes with synthetic underlayments saw about 30% less leaks and moisture-related problems within five years than those of felt underlayment. Moreover, synthetic materials composed of polypropylene and polyethylene are lighter to handle, therefore permitting faster installation, in turn cutting down labor costs by an estimated margin of 15%.
Adding to their list of pros is how they have slip-resistant surface properties, something that highly aids in the safety of installers on steep roofs. All of these improvements are appreciated since they’re good for the environment as some manufacturers incorporate recycled materials into the products.
Consequently, with all the mentioned advancements and the proving themselves in different real-world scenarios, synthetic roof underlayments promise an even larger somehow build on both residential and commercial building fronts.
Challenges Faced in Alternative Applications
While synthetic roof underlayments offer many positives, challenges continue in some alternative applications. One such challenge highlighted in recent insights is the initial higher material cost when contrasted with traditional felt underlayments. Some sources note the synthetic choices can cost two to three times as much, and that fact will dissuade set-up workers new to the field, as well as homeowners with budget constraints.
Furthermore, despite being very durable, installation errors can cause force concentration around fasteners and tear. In contrast, an industrial expert would say that UV exposure would degrade the material if it were left uncovered for a very long time. The majority of synthetic underlayments set their exposure rating roughly between 90 and 180 days. One would risk potential structural failure if they disregard that exposure time.
According to a 2023 industry survey, some 25% of contractors stated that they had experienced sourcing difficulties in synthetic underlayments that comply with region-specific building codes. Preparing for actual work would very often require additional research or adjustments. The solution is to pay attention to materials choices, select competent installers and follow the provided guidelines by manufacturers to ensure the material provides utmost serviceability in all applications.
Conclusion and Recommendations
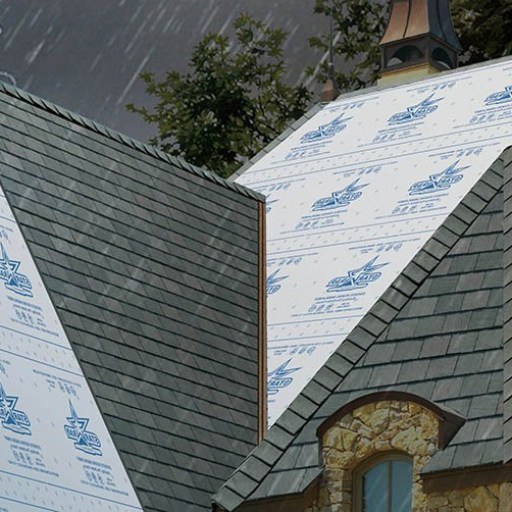
In handling the challenges that were mentioned, I focus on sourcing reliable synthetic underlayment from manufacturers in which I put my trust, ensuring that all local standards and codes of building are met, and planning a project meticulously while following manufacturer instructions as well as installation practices and techniques given by them that will give the best result to any particular project.
Best Practices for Using Synthetic Roof Underlayment
Some of the best practices to use synthetic roof underlayments include those to ensure that an efficient and long-lasting roof system is put up. In recent data, it has been stated that synthetic underlayments perform better in waterproofing as compared to the traditional felt materials, with many products having a water penetration performance rating that is 50% higher than the performances of felt materials. This durability offers a better way for underlayment in heavy rainfall or altered weather conditions in any given region.
Hence, synthetic underlayment that is very strong, yet quite light, is especially efficient during the installation process and reduce any excess strain that could be placed upon the building structure. Studies show that synthetic underlayment weighs 2 to 4 pounds per roofing square, whereas conventional felt may weigh over 15 pounds per square. This weight difference aids not only in ease of transportation but also in accelerated installation times, which means a saving on labor costs.
Therefore, underlayments with a high coefficient of friction would help maximize safety by reducing slips during installation on steep slopes. Some of the newest products have engineered advanced surface texture to achieve slip resistance.
Another consideration would be how resistant an underlayment is to the effects of UV rays. The majority of synthetic underlayments will endure direct sun exposure for 90 to 180 days without any significant deterioration, thus allowing quite lengthy construction schedules versus felt, which is usually only rated to withstand about 30 days of UV exposure.
Combining quality materials with good installation techniques-an example is overlapping sheets at least 4 inches and securing them tightly with corrosion-resistant fasteners-will help guarantee that the roofing system can do its job long enough. Observing the manufacturer’s directions is another crucial detail that could make or break warranties.
Final Thoughts on Choosing Between Underlayment and House Wrap
Deciding whether you’re opting for underlayment or house wrap entails knowing the difference in usage and how they’re likely to perform. Again, according to the latest data in the industry, such synthetic underlayments provide almost the best longevity and water resistance it could have in comparison with that of an asphalt felt. Its life spans anywhere from 20 and 40 years, according to the material used. At the same time, that makes it a very affordable long-term roofing solution. Furthermore, synthetic- underlayments tend to be lighter and are tear resistant, making them easier and quicker to install.
House wrap, however, is mostly employed to prevent moisture penetration while letting water vapor from inside the walls dissipate. Modern brands of house wrap such as Tyvek or ZIP System boast advanced breathability ratings with water vapor permeability estimated above 60 perms, which adds to effective moisture management. The feature minimizes the risk of mold growth and greatly improves energy efficiency by cutting down on air leakage; this statement is backed by research by energy efficiency experts.
Ultimately, the choice primarily depends on what your building project specifically needs. A good synthetic underlayment, for example, would do wonders for weather protection in roofing operations. Optionally, excellent, well-sealed house wrap can take care of wall moisture for the sake of long-term integrity and energy conservation. Always take in consideration the environment, the warranty of the materials, and the manufacturer’s recommendations before actually buying something.
Future Trends in Roofing and House Wrap Materials
The world of construction is evolving at a rapid pace aided by technological innovations and demands for further sustainable concrete designs and greater energy efficiency. This could lead to the concept of smart roofing materials with their additional features such as coatings for energy efficiency and solar panels. According to occurrence in the market, the global cool roofing material market is predicted to touch $10.4 billion by 2030, propelled due to the demand for proper thermal regulation of buildings.
House wrap materials, on the other hand, are undergoing advancements in moisture management and air barrier technologies. The newest top-performance house wraps are being brought out with enhanced vapor permeability while maintaining excellent water resistance, thus furthering durability and structural protection. Some manufacturers have started to launch eco-friendlier versions made from recycling or biodegradable materials to align with the growing consciousness of the environment in the construction industry.
Further, the integration with smart monitoring systems is increasingly common, allowing homeowners and builders real-time tracking of moisture levels and air leakage. The future of roofing and house wrap materials is boosted by this blend of sustainability, functionality, and technology, ensuring the long-term efficiency and resilience of modern buildings.
Reference sources
1. Research on Construction Materials
- Title: “Numerical Study of Integrating Thermal Insulation Local Bio-Sourced Materials into Walls and Roofs for Thermal Comfort Improvement in Buildings in a Tropical Climate”
- Authors: Kokou Dowou et al.
- Publication Date: 2025-01-22
- Summary: This study discusses the importance of using various materials for insulation and their impact on thermal comfort in buildings. While it focuses on bio-sourced materials, it provides insights into the properties of synthetic materials and their potential applications in building envelopes, including the use of synthetic underlayment as a moisture barrier(Dowou et al., 2025).
2. Building Science Insights
- Title: “Bringing Green Homes within Reach: Healthier Housing for More People”
- Author: C. Schmidt
- Publication Date: 2008-01-01
- Summary: This article discusses the integration of sustainable materials in home construction, including the use of synthetic materials for improved energy efficiency and indoor air quality. It highlights the role of synthetic underlayment in enhancing the performance of building envelopes, which can be relevant when considering its use as house wrap(Schmidt, 2008, pp. A24–A31).
3. Construction and Building Materials Review
- Title: “A Study on E-Learning Technology as Reliable Source of Knowledge Among Students in Nagpur City”
- Authors: R. V. Sontakay, A. Das
- Publication Date: 2021-12-31
- Summary: Although primarily focused on e-learning, this study touches on the importance of reliable information sources in construction practices. It emphasizes the need for accurate knowledge regarding building materials, which can include discussions on the properties and applications of synthetic roof underlayment in various contexts, including its potential as a house wrap(Anshori et al., 2023).
Frequently Asked Questions (FAQs)
Can synthetic roof underlayment be used as house wrap?
Yes, synthetic roof underlayment may be used as house wrap. Linear synthetic roof underlayments are designed to be water resistant and durable to be used in roofing as well as wall applications. The important caution that must be exercised is making sure that the exact product you wish to use would be accepted under local building codes for use as house wrap.
What are the HVAC advantages of using synthetic roof underlayment instead of building paper?
Synthetic roof underlayment provides some benefits above traditional building paper; it is more water-resistant, durable, and lighter. Synthetic alternatives are also sometimes permeable, which allows vapor to pass but restricts water and air penetration, thus reducing moisture problems within the wall assembly.
Is synthetic roofing underlayment a good air-sealing membrane?
If installed properly, synthetic roofing underlayment can be part of an air-sealing system because it creates an air barrier against airflow and moisture infiltration, toward making a home more energy-efficient by limiting drafts and the potential for condensation within the wall assembly.
Can synthetic underlayment be installed on a sloped roof?
Yes. Synthetic underlayment is especially beneficial on sloped roofs: Its slip resistance is excellent, and it remains in position through the rigors of installation, thereby protecting the roof panels from water infiltration caused by rain or snow.
How is synthetic roof underlayment different from felt-paper?
Synthetic roof underlayment will usually out-perform felt-paper in the matters of water resistance, weight, and longevity. The felt-paper absorbs moisture and consequently may degrade while the synthetic are actually made of fibers – polypropylene or polyethylene – which make for a waterproof barrier for a longer time, less resistant to mold and mildew.
What alternatives to synthetic underlayment exist for roofing?
Other alternatives do exist to the synthetic underlayment; the most usual types are the traditional asphalt-saturated felt, tar paper, and some types of building paper. Each choice has its opportunities and hazards, but for waterproofing and durability, synthetic underlayment is most often chosen.
What considerations should be given when choosing between a synthetic roof underlayment and a house wrap?
This choice has to be made in conjunction with such considerations as the building application in question, local building codes, and the materials’ ability to resist water and air infiltration. Buildings assemble these materials in ways which interact with the roofing panels and siding in order to provide a comprehensive moisture management approach.
Will synthetic roof underlayment insulate my home?
Not really, synthetic roof underlayment is mostly not an insulating product and so can merely increase the overall thermal performance of your home by fighting against air leakage or moisture problems. This could therefore enhance energy efficiency if installed properly with wall and roof insulation.