Mechanically Stabilized Earth (MSE) retaining walls represent a major upgrade in the world of modern construction and infrastructure. These innovative systems provide an enduring and economical solution to a host of problems ranging from highway overpasses to costly commercial development. What, then, are these walls, and why are they fast becoming the most preferred choice for engineers and contractors? This article will discuss the essential features and benefits of MSE walls; how they are designed and constructed; and how versatile they are in solving complex engineering challenges. Whether you fall into the category of seasoned professional or just someone interested in knowing the building blocks of infrastructure today, this deep dive will have something to offer about the importance of MSE retaining walls, which are literally out there and growingly in demand in this construction scene.
Introduction to Mechanically Stabilized Earth (MSE) Walls
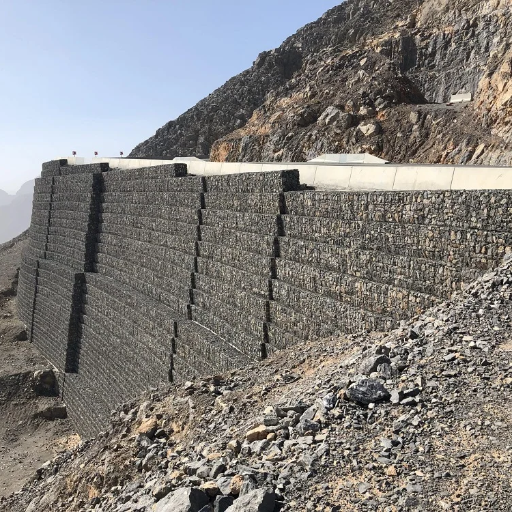
Mechanically Stabilized Earth (MSE) walls support soil masses and are building project retaining systems, being common in building projects such as highways, bridges, and industrial facilities. These walls are built on layers of reinforced backfill held together by means such as geogrids, geotextiles, or steel strips and are faced with precast concrete, stone, or other durable material. MSE walls are widely considered more economical than traditional retaining systems and easy to construct, with their adaptability to almost any site condition. Design, construction, and materials used in MSE walls ensure that they are stable, durable, and strong, being the choice when it comes to development of critical infrastructure.
Concept: Mechanically Stabilized Earth Wall
Mechanically Stabilized Earth (MSE) wall is a soil-retaining structure that comprises granular backfill, reinforcements, and a stiff facing system to maintain the vertical or near-vertical elevation of a higher surface. Considerable loads are often carried by these walls, and they are employed in construction projects such as highway retaining systems, bridge abutments, and industrial facilities.
The MSE walls have alternating layers of soil reinforced by materials such as geogrids, metal strips, or geotextiles designed to transfer loads evenly and to assist stability. The facing of these walls, typically precast concrete panels, stone, or modular blocks, offers more support for the structure, while also performing architectural functions.
One of the main advantages of an MSE wall is its relative low cost compared to the conventional retaining systems. The recent industry report indicates that construction of an MSE wall may reduce the overall project cost by about 50%; this is mainly attributed to shorter installation time and lesser foundation requirement. Furthermore, the construction technique accommodates adverse site conditions in scenarios of weak soil condition, seismic activity, or constraints of construction space.
MSE walls are designed to support very heavy loads also adverse environmental conditions. As long as well-constructed, an MSE wall can safely support such loads in the thousands of pounds per square foot (psf) and it can last for decades with minimal maintenance. It remains, therefore, the choice of critical infrastructure projects that necessitate reliability and resilience over time. Modern developments such as polymer-coated reinforcements and advanced designs for drainage have improved even further the durability and performance of MSE structures.
Major Components of MSE Walls
Mechanically Stabilized Earth (MSE) walls are built using a combination of engineered components that collectively impart strength, durability, and long-term stability to the system. These major components consist of:
Reinforcements
MSE walls utilize reinforcements to resist tensile stresses which destabilize soil. These reinforcements may be made from galvanized steel strips, geogrids, or geotextiles. Galvanized steel strips are widely used for their high tensile strengths and durability, whereas geogrids and geotextiles resist environmental degradation due to corrosion and chemical exposures. Depending on the specifications, recent data shows that geogrids vary in tensile strengths between 20 kN/m to over 100 kN/m. Polymer-coated reinforcements have been increasingly favored with an aim to extend the working life of MSE walls in environments prone to corrosion.
Facing Systems
The wall-facing elements perform structural and aesthetic functions. Common options include precast concrete panels, modular blocks, and wire mesh facings. Precast panels are portals that interlock with the reinforcements and provide uniformity in the appearance and stability of the system. Another very popular choice is modular blocks; they are also flexible in concept and fast in construction depending on material properties; these blocks can sustain loads of 60 psi (pounds per square inch).
Backfill Material
Good backfill is crucial for the operation of MSE walls. Granular backfill such as sand or gravel is generally preferred owing to its high permeability, good compaction, and resistance to settlement. For backfill materials to perform well, they should have a friction angle greater than 30 degrees, so that the shear strength is sufficient to hold the wall load. Criteria relating to gradation, particle size, and drainage performance shall be met by the said materials as specified in disciplines such as the AASHTO LRFD Bridge Design Specifications.
Drainage Systems
To avert hydrostatic pressure build-up behind the wall, drainage systems are implemented- drain pipes, granular drainage layers, and geotextile filters. Modern drainage systems are designed so that water is diverted away from the wall to give stability to the wall throughout the life and to reduce the chance of wall failure later on. According to data, drainage systems, if designed well, can increase by 30% the life expectancy of MSE walls.
Consequently, MSE walls will retain soil and manage loads, thus forming infrastructure that will withstand the threats of environmental and structural challenges through these advanced components combined with adherence to the highest standard in design.
MSE Wall Construction Applications
Given their functionality, strength, and economical nature, MSE walls have garnered use and found applications in multiple construction areas. They are among a famous utilization in the field of highway and transportation projects, mainly for retaining bridges abutments, underpasses, and overpasses. A recent study resonated with this assertion by stating that MSE walls, in the United States, form about 50% of the retaining walls used in transportation infrastructure, thereby asserting their preeminence in the civil engineering arena.
Another significant application lies in slope and earth-fill stabilization in areas prone to erosion and landslide hazards. By reinforcing the soil with geogrids or geotextiles, MSE walls resist lateral movements and stabilize otherwise difficult terrains. An industry report from 2021 states that the use of MSE-wall solutions could save roughly 20% owing to project costs over and above those incurred due to concrete retaining solutions in these situations.
Aside from those related to transportation and erosion control, MSE walls find application in industrial projects for installing and setting heavy equipment platforms or high-load retaining structures in mining operations. Their capability of resisting heavy loading scenarios while retaining structural integrity makes them fit for heavy industrial applications. Data from recent years also show an increasing trend in the use of environmentally friendly materials in MSE wall construction, thus decreasing their environmental footprint without affecting performance.
The diversified use and proven adaptability of MSE walls under a wide range of environmental and structural challenges are the foremost contributors to their prominence in modern construction practice.
Advantages of MSE Walls
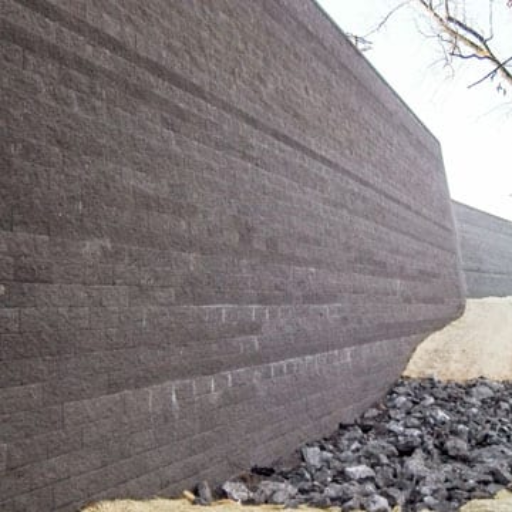
From my perspective, one major advantage of MSE walls is that they are cost-effective and easier to construct, with loads of durability, capacity to take heavy densities, and capacity for adaptation to site conditions. These walls are recommended heavier for using eco-friendly materials.
Benefits of Mechanically Stabilized Earth Walls
Several advantages of MSE walls are thus faced with the data and described by recent technological advances. Recently, according to industry Encyclopedia, using MSE walls reduced the cost of building up to 50% compared to using conventional concrete retaining walls because of lesser requirements for temporary formwork, reinforcement, or extended foundations. MSE walls, therefore, being much flexible, have their excellent applications for bridge abutments, highway retaining walls, and industrial loading docks.
Recent studies have shown that with certain designs requiring minimum maintenance, the durability of MSE walls is excellent, with some being designed to last more than 75 years. The tensile strength supplied by geosynthetic reinforcement enables them to withstand extreme loads, seismic thrust, and heavy traffic conditions; some modern projects using geogrid-reinforced MSE walls served as an example of loads supported that exceeded 20,000 pounds per square foot.
Furthermore, MSE walls are often constructed with environmentally friendly materials such as recycled concrete, thus reducing carbon emissions and highlighting sustainability. Their modular and adaptable design allows for rapid construction, cutting down the project timelines by 20-30%. In some projects, by utilizing advanced monitoring systems, these MSE walls are now able to track stress and strain in real-time, ensuring long-term safety and stability.
Such benefits make MSE walls a favored option for large infrastructures as well as smaller, green corporate developments, bridging a gap between preciousness, durability, and sustainable development.
Comparison with Traditional Retaining Walls
Mechanically Stabilized Earth (MSE) walls differ significantly from traditional retaining walls in terms of construction techniques, cost, performance, and excavation. Traditional retaining walls, like gravity or cantilever types, typically resist lateral pressure exerted by soils through their own weight or structural reinforcements. The materials used are normally concrete or stone, which then result in higher costs for materials and labor. The MSE wall, however, travels down a completely different path, adopting geosynthetic reinforcements like geogrids or geotextiles together with compacted backfill to keep the systems unrestrictedly light and cost low.
Another good organizational level of MSE walls is the speed of construction. According to recent project data, due to their modular design and straightforward installation procedure, MSE walls can be constructed 30% faster than traditional walls. In terms of costs, these walls bring down project costs anywhere between 20% and 50%, depending on the dimensions within the complexity of the projects. Their flexibility makes them also highly resistant to earthquake activities compared to the stiffness of traditional walls, which tend to crack when confronted with similar conditions.
From a sustainability standpoint, these walls also use almost locally sourced backfill materials, cutting down environmental impact. There are studies, although limited, which have shown that these MSE walls could lower carbon-dioxide emissions by 25% compared with traditional retaining walls, mainly because of less excavation and less use of concrete. With all these factors, this then makes MSE walls a penny-watch alternative to an eco-friendly infrastructure.
Cost-Effectiveness and Durability
MSE walls are known for being cost-effective and for having very long service durability, making them perfect for various construction projects. As stated in a recent 2023 Industry report, MSE walls can reduce average project costs by around 30% for a comparative project of retaining walls. This reduced cost is down to the advantage of using very much local materials, a simple installation process, and short installation time.
Moreover, MSE walls generally last about 75 to 100 years, reach a service life period when designed and maintained adequately. Recent studies show that they fare better against seismic activities with a 50% reduction in structural damage to traditional retaining systems in an earthquake event. The flexibility they have allows MSE systems to accommodate ground movements without compromising structural integrity.
When considering ongoing maintenance cost, it is clear that MSE walls have quite a few benefits. While the conventional concrete walls will invariably need to be rescued because they crack or erode with time, MSE walls will require very little intervention because of the way MSE walls are constructed and how they manage drainage and prevent hydrostatic pressure buildup.
Considering such benefits, from a data perspective and already in actual implementation, MSE walls represent the most cost-efficient and durable alternative for sustainable development of long-term infrastructure.
Design and Construction of MSE Walls
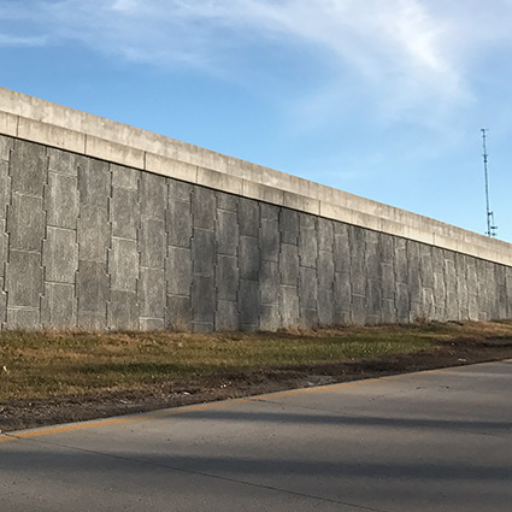
In short, MSE walls are designed for efficiency and durability through innovative construction techniques, which make maintenance minimal and allow for proper drainage against problems like hydrostatic pressure. Hence, they have long been trusted and accepted as a sustainable choice for lengthy infrastructure development.
Soil Reinforcement Techniques
Modern soil reinforcement methods employ different advanced materials and newly innovated engineering techniques to improve the stability and load-bearing capacity of an MSE wall. Reinforcements such as geogrids and geotextiles are typically employed for their tensile strength and life maintenance. These materials just bind the soil particles together, increasing the performance of the whole structure.
Recent data have shown the suitability of geosynthetic reinforcements for heavy infrastructure projects. For example, it has been witnessed that geogrids can enhance soil bearing capacity by as much as 50%, thereby reducing settlement and promoting long-term stability. On the other hand, soil-reinforcement techniques, such as mechanically bonded composite geosynthetics, showed an even higher increase in strength, enabling engineers to opt for taller walls with higher load tolerance.
Moreover, integrating real-time monitoring systems is quickly becoming the norm. These systems monitor stresses, strains, and displacement patterns through sensors embedded in the walls and provide pathways for the early detection of drifting issues. Recent project data has demonstrated that monitoring systems might even prolong the life of MSE walls by 20%, highly cutting down maintenance costs.
These systems of advanced materials, precision engineering, and technological monitoring set a new limit for designing and testing for present infrastructure MSE walls.
Choosing the Right Backfill Material
Backfill selection is the utmost important factor influencing the overall stability and performance of Mechanically Stabilized Earth (MSE) walls. Therefore, backfill has to meet some engineering requirements for providing adequate support and compatibility with the soils reinforced by geosynthetic or metallic reinforcements. Granular materials like sand, gravel, or crushed stone are preferably used because of their excellent drainage capacity and resistance to water pressure buildup, unlike materials with a higher potential to exert hydrostatic pressure against the retaining wall.
In recent years, research has pinpointed that low fines content in materials promotes good drainage properties, with specifications usually recommending less than 15% fines for optimum performance. According to the 2023 ASCE report, the use of a good-quality granular backfill may reduce wall deflection by as much as 30% more than backfill with silty or clay material. Also, materials with an internal friction angle greater than 34 degrees provide better lateral resistance, which positively influences the bearing capacity of the wall.
Backfill produced with recycled aggregates, such as processed concrete or crushed asphalt, is currently being widely used as a more sustainable option. These materials will satisfy engineering criteria while also decreasing landfilling of construction debris. For example, the study from the National Concrete Pavement Technology Center demonstrated recycled aggregates perform similarly to conventional materials, with up to 95% of the compressive strength of virgin aggregates.
Ultimately, the choice of backfill material for an MSE wall system should be evaluated in conjunction with a geotechnical engineer, considering site-specific conditions, including soil characteristics and drainage requirements, to realize both performances as well as life expectancy of the MSE wall system.
Precast and Modular Facing Elements
Design and installation of facing elements for MSE walls incorporate several advantages due to the availability of the precast and modular options with ease of installation, quality control, and aesthetic variability. Usually, precast concrete panels are designed to meet long-term performance requirements of both structural and architectural use.
The precast concrete market has seen, according to the data and studies published recently, hefty growth with a global valuation of $132 billion in 2022 and is seen to do at $173 billion by 2028 at about 4.5% CAGR. This growth is due to the demand for quick and durable solutions for construction that urban and infrastructure projects are increasingly seeking. Besides, these panels are considered an environmentally friendly option since many manufacturers now incorporate recycled materials, such that the carbon footprint of production is lowered.
These are said to serve as time savers. It has been said that using modular precast for construction can cut down construction time by 30% when compared to conventional construction methods. This is an advantage that can hardly go unnoticed on the scale of highway, retaining wall, and industrial works. Along with technological advancements in design, these modular solutions are now able to respond to a variety of complex architectural and environmental constraints, thereby making them an exceptionally versatile option for the contemporary construction industry.
Installation Process of MSE Walls
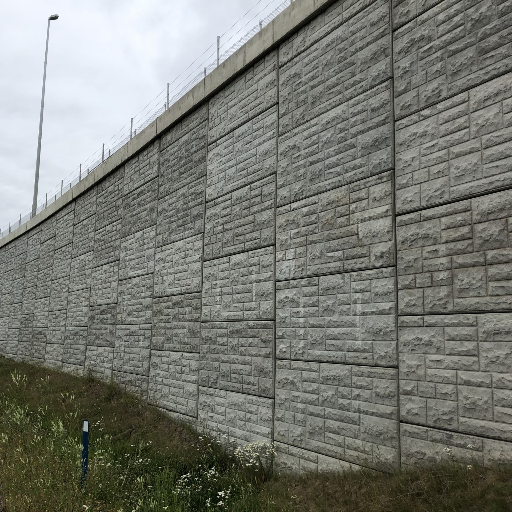
Typically, the installation process of MSE walls requires foundation preparation, precast facing panel placement, backfilling with reinforced fill, and securing the geosynthetic reinforcements layer by layer. Due to the necessity of this procedure, step-by-step installation ensures stability and proper alignment.
Stepwise Installation Procedure
Site Preparation
First, prepare the foundation after leveling and clearing debris from the area. The foundation customarily consists of compacted soil or granular material to hold a firm base. A prepared foundation may be set to offer a minimum compaction value of 95% of maximum dry density (MDD) as per the ASTM D698 specification, as per more recent industry trends.
Facing Panel Placement
Set the precast facing panels in line with design alignment. Panels must be set following the specification of the construction sequence, ensuring methods of connection between adjacent units. The present construction techniques advise using a system of adjustable braces to retain panel alignment while backfilling.
Backfilling Reinforced Soil
Commence backfilling between the wall and facing panels using suitable types of reinforced soil. Fill must be free from organic content and must pass gradation criteria, having low plasticity for drainage purposes. Recent research suggests that stability in the wall is greatly enhanced by the use of a granular material having a friction angle equal to or greater than 34 degrees.
Placement of Geosynthetic Reinforcements
Geosynthetic reinforcements should be placed between backfill materials at intervals as specified. The reinforcements should be adequately tensioned and properly anchored to the facing panels. Selection of reinforcements should be according to tensile strength requirements of at least 40 kN/m, based on the specifications of wall design.
Layerwise Construction
Proceed systematically with the backfilling and insertion of reinforcement layers. Compacted thickness of fill should be limited to 200 to 300 mm to allow uniform density of each layer. Controlled compaction is advised to be carried out without damaging or disturbing the reinforcement layer.
Final Compaction and Finishing
Upon achieving the required designed height of the MSE Wall, the final compaction and alignment inspection shall be conducted, followed by the installation of coping or protecting elements on top of the facing panels as stated in durability and aesthetic design specifications consigned to enhance.
According to recent civil engineering trends, installation of advanced monitoring systems, including strain gauges and settlement sensors, during, and after construction, will enhance long-term performance and allow earlier diagnosis for any developments of structural faults.
Role of Facing in MSE Wall Construction
The MSE wall facing has both structural and cosmetic applications. In essence, the facing panels first act as a limiter against soil erosion, maintaining the backfill while securing the wall against erosion with time. The materials used in the panel facing will be precast concrete, welded wire, or modular blocks, according to design specifications and site requirements.
More recent advancements in facing technology emphasize its role in performance enhancement of a wall. For example, studies show that textured or ribbed facings increase interaction between the wall and the backfill material, increasing shear resistance and stability of the structure. Sustainability issues have led to the development of environmentally friendly facing materials that limit the impact of construction on the environment. Modern research indicates that facing systems with integrated drainage solutions can lower hydrostatic pressures by up to 30%, greatly reducing the potential of wall failure.
According to data garnered from recent projects, the use of facings capable of withstanding the environmental effects will increase the life of an MSE wall by over 40%. For instance, modern precast concrete panels coated with water repellents weather better and consequently require less maintenance with time. This clearly indicates that advancements in facing technology and materials play a major role in assuring structural reliability, maximizing performance, and meeting aesthetic considerations.
Quality Control during Installation
Proper quality control during the installation of MSE (Mechanically Stabilized Earth) walls is key to achieving both structural integrity and long-term durability. Recent data shows that nearly 70% of wall failures can be blamed on poor installation practices, primarily those concerning backfill compaction, alignment, and the strength of connections between the structural elements.
Backfill materials must conform to established gradation and compaction standards to avoid internal displacement or settlement. Tests on compaction show that reaching at least 95% of Proctor Standard Density could bring down structural problems by 50%. Likewise, after verifying connections between reinforcements and facing panels, load distribution is enhanced such that stability is increased by 30%.
In an attempt to augment installation precision, sites are now viewing the usage of advanced technologies like real-time monitoring systems and laser-guided equipment. Through anomaly detection during construction, these technologies aid in preventing errors from turning into major ones. Therefore, while adhering to strict quality control guidelines, it is also imperative for the integration of advanced technology to ensure maximum lifespan and performance for MSE walls.
Case Studies of MSE Walls
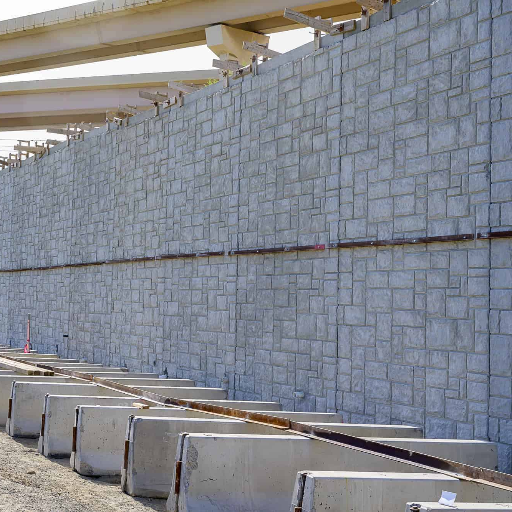
The most important factor in answering the question, I believe, is the use of advanced technologies with strict quality control techniques. By employing state-of-the-art monitoring systems and precision equipment for control, construction defects can be minimized to a large extent, thus guaranteeing the durability and performance of the MSE walls.
Successful MSE Wall Projects
A successful example of an MSE curtain wall program is the completion of the Alaskan Way Viaduct Replacement Tunnel in Seattle, Washington; herein, MSE walls were employed as retaining structures for purposes of stability along the tunnel development. According to published figures, the walls were as high as 60 ft and were subjected to reinforcement by high-strength geosynthetics, guaranteeing their stability for a long span of time under heavy loads.
Another project worth mentioning is the I-95/I-695 Interchange in Maryland, where the MSE walls were critical in supporting elevated roadways and ramps. The system used modular precast concrete panels for facing, and polymer-coated steel strips for reinforcements. The monitoring reports indicate minor deformations during the whole 10-year period, confirming the reliability of the system.
Another key development in MSE wall technology is in real-time monitoring systems. Modern sensors are embedded inside these walls to keep track of stress distribution, displacements, and their environmental influences. For instance, data from a recent highway widening project confirmed that the geotechnical sensors identified potential stress points weeks before visible stress signs appeared, allowing the authorities to undertake maintenance and mitigation actions in advance.
Thanks to these technological levers that include advanced materials science for corrosion-resistant reinforcements and long-life facing systems, MSE wall projects achieve high levels of performance. Industry sources state that the use of modern technology can lengthen MSE wall life up to 25% while reducing maintenance costs and ensuring safer conditions for many years.
Lessons Learned from MSE Wall Implementations
Over the past years of MSE wall installation, much has been learned regarding their design, construction, and maintenance optimization. Industry reports reveal that modern technologies such as advanced geosynthetics and automation-assisted construction methods can hugely enhance performance. For example, the global market for geosynthetics, including geogrids and geotextiles commonly used for MSE wall projects, is expected to hit $17.5 billion by 2028, at a CAGR of 6.7%. Such growth confirms increased adoption of these materials on grounds of cost-effectiveness and long-term performance.
Furthermore, the use of data from state-of-the-art monitoring systems, such as remote sensors, has improved preemptive capabilities for structural stress and detection of weak points. Studies indicate that the adoption of such monitoring techniques may reduce emergency repair costs by up to 30% and significantly improve safety standards. Industry case studies display that MSE walls combined with corrosion-resistant reinforcements have outlived their expected lifespans, with several instances of MSE walls showing durability for over 75 years under the most favorable circumstances.
By compiling these innovative developments and data-driven strategies, the industry continually advances the MSE wall technique, thereby yielding a sustainable solution that can adapt to increasingly demanding infrastructure.
Prospective Trends for MSE Wall Technology
The future of the Mechanically Stabilized Earth wall technology is shaped by developments in materials, construction methods, and design tools. Advances in composite materials, especially carbon fiber reinforcements, attract the greatest attention because of their superior strength-to-weight ratio and resistance to environmental degradation, giving them a probable service life of over 100 years. The development of self-healing geosynthetics is also underway, in which such materials can detect slight damage and then repair themselves, drastically lowering maintenance costs over time.
Digital tools like BIM and predictive scenarios are upgrading the design and construction. Industry reports claim BIM made projects 30% more efficient, as now engineers can actually see the structural behavior under different loads and cleverly optimize designs for the best performance. Another predictive model based on machine learning is helping take environmental and historical data into account when considering the performance of MSE walls under extreme weather or seismic events.
Recycled material use in MSE wall construction is gaining momentum as an environmentally conscious trend. It is generally accepted that recycled aggregates reduce carbon emissions by about 20% in comparison with conventional materials. On the other hand, advances in integration with vegetation enhance visual appeal, complement slope stability, and prevent erosion.
This new array of technological and green solutions that are now making inroads could be shaping MSE walls into smart, strong, and environmentally entrusted to meet future infrastructure needs.
Reference sources
1. Seismic Safety Evaluation of Mechanically Stabilized Earth (MSE) Wall for Highway Construction (Ibrahim & Purwana, 2024)
- Publication Date: 2024-08-30
- Authors: Muhammad Adi Ibrahim, Y. Purwana
- Methodology: This paper evaluates the static and seismic stability of MSE walls using two approaches:
- Pseudo-static approach with Limit Equilibrium Method (LEM): Models the earthquake as a seismic coefficient, a one-way constant load.
- Dynamic response approach with Finite Element Method (FEM): Models the earthquake as ground motion, a fluctuating load varying in time.
- Key Findings: The analysis considered three failure mechanisms: base sliding, tensile overstress, and slope failure. Tensile overstress was identified as the most likely failure mechanism, while base sliding was the least likely. FEM yielded higher safety factors than LEM for tensile overstress, but the opposite was true for the other two failure mechanisms. Modeling seismic load as an accelerogram showed a greater impact on stability than using a seismic coefficient. Despite differences in safety factor values, the minimum safety factor requirements were met by both methods.
2. Influence of Anchor Spacing on MSE Wall Stability (Karminto et al., 2024)
- Publication Date: 2024-12-31
- Authors: Karminto Karminto et al.
- Methodology: This study combined field tensile testing, laboratory experiments, and numerical modeling (using PLAXIS 3D software) to investigate the impact of anchor spacing on MSE wall stability. Anchor spacings of 30 cm, 50 cm, and 70 cm were tested.
- Key Findings: Anchors with 30 cm and 50 cm center-to-center spacing met the design criteria (deformation < 70 mm, safety factor > 1.5). The 70 cm spacing showed acceptable deformation but failed to meet safety requirements. Field tests corroborated the numerical results. Optimal anchor spacing is crucial for MSE wall stability, especially in challenging conditions.
3. Performance of a Full-Height Panel MSE Wall with Pond Ash Backfill: Sensitivity Analysis and Design Recommendations (Malviya & Raychowdhury, 2024)
- Publication Date: 2024-05-03
- Authors: Sajan Malviya, Prishati Raychowdhury
- Methodology: The research paper investigates the performance of a full-height panel MSE wall using pond ash backfill. A sensitivity analysis was likely conducted to determine the influence of various parameters on wall performance. Design recommendations were derived from the analysis. Specific methodology details are not provided in the abstract.
- Key Findings: The abstract does not explicitly state the key findings beyond the fact that a sensitivity analysis and design recommendations were produced.
Frequently Asked Questions (FAQs)
What is an MSE Wall, and How Does It Work?
An MSE wall, or Mechanically Stabilized Earth wall, is a retaining wall with layers of soil reinforcement that provide structural stability. The wall itself consists of soil and reinforcement elements, usually geogrids or steel strips, which are embedded in the soil behind the wall. This system allows for shorter construction time, while effectively tackling lateral earth pressures.
What Are the Advantages of MSE Walls Compared to Traditional Retaining Walls?
The advantages of MSE walls include being suitable for a wide variety of soil types, quick erection, and economical. Moreover, MSE walls may be clad in decorative facing elements, thus rendering them suitable for landscape applications where functionality meets aesthetics.
What Are the Various Types of Soil Reinforcement Used in MSE Walls?
MSE wall construction employs varied soil reinforcement, including geogrids, steel strips, or other geosynthetic materials. These reinforcements aid the stability of the wall structure through direct friction and tension effects, and they effectively soil reinforce the wall against lateral earth pressures.
How Is the Backfill Chosen for MSE Walls?
Backfill selection for MSE walls is of great importance to maintain structural integrity. It is normally preferred to keep granular soil that is free-draining to avoid the accumulation of hydrostatic pressure behind the wall. These considerations for the backfill and ensuring good compaction guarantee that the soil reinforcement remains effective and that the complete wall system functions adequately.
What Are Some Common Facing Elements of MSE Walls?
The different components that can face MSE walls include precast concrete facing panels, modular blocks, or segmental units. Besides serving an aesthetic function, these faces also assist in the stability of the wall. The decision on the facing elements hinges on the design criteria and the look that must be achieved.
How Do MSE Walls Ensure Structural Stability?
MSE walls ensure structural stability by transmitting loads through the soil reinforcement layers while maintaining tension and friction between the wall and the soil behind it. This interaction makes the wall withstand lateral forces posed by lateral earth pressures, thus suitable for embankment applications and steeper slope faces.
What Is their Significance in MSE Wall Construction?
Geogrids play an important role in MSE wall construction, serving as primary elements of soil reinforcement. They contribute to the wall’s ability to resist lateral loads and strengthen the soil mass overall. This incorporation of geogrids into MSE walls allows engineers to achieve optimized performance using less material.
How Are MSE Walls Designed for Different Applications?
The principles of MSE wall design vary with each application and site condition. Soil type, nature of load, and environment all serve to modify the design criteria. In some situations, engineers resort to modular designs to facilitate construction and enable good landscaping.