Landfills form an essential part of waste management, but since waste management has to be effective and environmentally sound, the construction has to be done carefully using the proper technology. Among other things, a geosynthetic liner system is one critical feature useful for achieving this balance. These new materials provide a barrier against contaminants entering the soil and water systems. Today, let’s talk about the significance of geosynthetic liners in landfill containment, how they work, and the various types thereof. Whether you’re a professional environmentalist or just a curious mind about the new-age way of tackling waste, this article will throw some light on how engineering protects our environment.
Introduction to Geosynthetic Landfill Liners
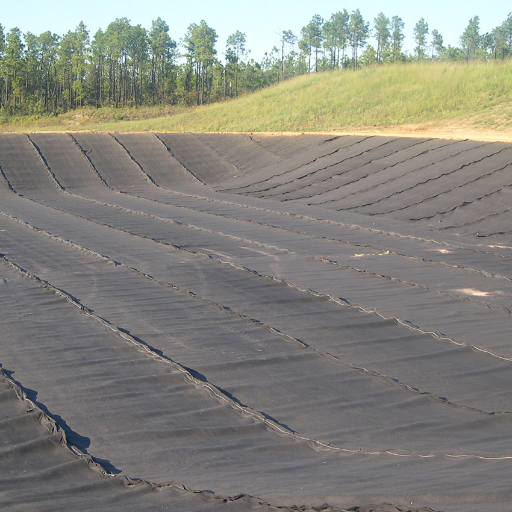
Geosynthetic landfill liners remain layers of engineered materials inserted in order to protect the waste and harmful substances from contaminating their surroundings. While the liner acts as a barrier between the waste and the soil, it prevents liquids and gases from escaping the landfill. Usually, in manufacturing, they are durable plastics or geomembranes-the liners are vital to landfill management to mitigate environmental hazards and secure contaminants from waste.
What are Geosynthetic Landfill Liners?
The geosynthetic landfill liners operate on purposely imparted roles in waste management today. They generally comprise synthetic polymers such as HDPE (high-density polyethylene), LLDPE (linear low-density polyethylene), or polypropylene, which poise themselves to be impermeable and also resistant to chemical degradation, attack by ultraviolet rays, or puncture. The liners serve the purpose of preventing the seepage of leachate, the liquid generated by the decomposition of wastes, into nearby soil and groundwater.
Geosynthetic liners are combined with other ingredients to form barriers, including compacted clay layers and leachate collection systems. However, according to industry data, HDPE geomembranes are the most commonly used due perhaps to their durability, with adequate maintenance, their longevity can surpass 30 years. More recently, multi-layered composite liners have been introduced which mix geosynthetics with geotextiles or geonets, therefore enhancing their structural and containment efficiencies.
Research concludes that these geosynthetic liners presented a leakage rate as low as 1 mm per year under good installation and maintenance conditions. They are also beneficial in greatly reducing the risk of contaminating the groundwater, satisfying strict environmental standards such as those set forth by the US Environmental Protection Agency (EPA). These include a hazardous waste landfill, a commercial solid waste landfill, mining applications, and wastewater treatment facilities.
In this case, landfill liner systems enable waste management systems to meet regulatory requirements while reducing and mitigating environmental and health effects of waste disposal; further advancements of the systems signify the effort of applied research and engineering-type solutions toward the goal of sustainable environmental engineering.
Waste Containment Importance
Waste containment plays an important role in environmental and public health protection. When no containment system exists, pollutants emanating from landfill sites seep into the surrounding soil and water bodies, thus posing contamination risks to ecosystems and human communities. Notably, studies have established that inappropriately managed waste accounts for about 3% of total greenhouse gas emission worldwide, mostly through the release of methane from decomposed organic materials in open dumps or unlined landfills. This is a clear indication of the need for containment measures to prevent or reduce environmental hazards.
Modern engineering solutions such as geosynthetic liners and leachate collection systems play crucial roles in waste containment strategies. It is stated that recent research values said reduction effect of using HDPE liners as high as 99%, thus abating contaminants in soil and groundwater. Also, as of 2023, landfill facility design, construction, operation, and monitoring are placed under strict requirements by regulatory bodies such as the US Environmental Protection Agency (EPA) to ensure that waste containment systems adhere to safety standards.
Corporate investment on the latest in waste containment will not just ensure compliance to mandated regulations but more towards sustainability goals. For example, landfill gas recovery implementation allows facilities to capture landfill methane emissions and convert them into usable energy. Worldwide, the leading landfill gas recovery projects have an advantage of uprooting and castrating millions of tons of CO2-equivalent emissions annually-the now-by-now that create a foothold for waste management technologies in combating environmental issues and supporting energy transitions.
Liner Systems Overview
These liner systems function in critical ways within the context of modern waste management by preventing the contamination of soil and groundwater from waste leachate. Mostly in landfills, they consist of a multi-layer barrier system, which extends from geosynthetic clay liners (GCLs) to high-density polyethylene (HDPE) membranes. Recent advancements have proven to equip the composite liner system with near-zero leakage rates, thus greatly enhancing protection of the environment.
According to studies, leakage of leachate would be diminished by over 99% in a properly designed and adequately maintained system of liners, thus meeting the environmental requirements. The Environmental Protection Agency, for instance, prescribes a double-liner system for municipal solid waste landfill sites combining primary and secondary barriers with leachate collection systems. It has been demonstrated that such systems can hold thousands of gallons of liquids per acre per day, thereby reducing the possibility of groundwater contamination.
Furthermore, state-of-the-art monitoring techniques are presently offered that can enable operators to detect and accurately locate potential failures of the liner in time to carry out proactive maintenance. This ensures that long-term functionality is pursued, thus flushes the landfill operation into the sustainability movement and further reduces the environmental impacts of waste disposal activities.
Types of Geosynthetics Used in Landfill Liners
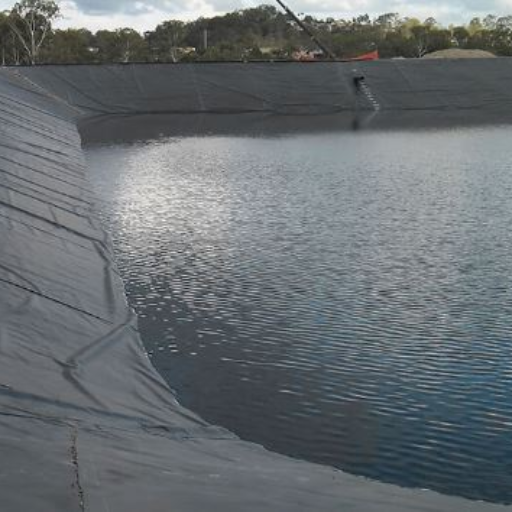
Prominent types of geosynthetics used in landfill liners are:
Geomembranes- They are impermeable liners manufactured from substances like HDPE to prevent the leakage of liquids.
Geotextiles- These are permeable fabrics used for filtration, separation, or reinforcement, usually in combination with other materials.
Geonets- They provide drainage by means of liquid flow within the liner system.
Geosynthetic Clay Liners-Which consist of layers of bentonite clay, functioning to increase barrier efficacy in combination with geomembranes.
Together, these materials provide containment and protection from environmental effects.
Working Understanding of Geosynthetic Clay Liners (GCLs)
Geosynthetic clay liners (GCLs) are advanced barrier systems used for containment and environmental applications. They are made of a thin layer of bentonite clay sandwiched between two layers of geotextiles or bonded to a geomembrane. Bentonite is a natural clay material with a high rate of swelling capacity and low permeability that can well mitigate fluid migration.
According to recent data, GCLs have exhibited hydraulic conductivity as low as 5×10⁻¹² meters per second, making them the best barrier to infiltration from water and chemicals. They are generally used in landfill lining, mining, and wastewater treatment facilities due to their cheapness and ease of installation compared to compacted clay liners. It is found that GCLs may decrease leakage by up to 70% in combination with high-density polyethylene (HDPE) geomembranes.
Recent developments focus on improving the durability of GCLs under extreme environmental conditions. For instance, to enhance resistance to chemical degradation, polymer-enhanced bentonite formulations are being developed. With an increasing emphasis on sustainability, GCLs will continue to be an integral factor in shielding soil and water resources from contamination.
Geomembranes: HDPE and Further
Geomembranes, with those made from HDPE withstanding exceptional water containment capability and chemical attacks, are considered best. HDPE geomembranes usually last for more than 30 years; hence, they provide a good and durable membrane solution for landfills, mining, and water storage. Some of the most recent innovations in the construction of membranes include the textured HDPE geomembrane, which increases the discrepancy angle for better efficiency and safety on difficult terrain.
The industry data suggests that HDPE geomembranes have a tensile strength of nearly 30 kN/m and an elongation at break of over 700%, while materials under stress have better mechanical properties. Also, modern-day geomembranes are manufactured with UV protective compounds that hinder degradation upon exposure to sunlight for inordinate periods; this feature is paramount for applications planned for arid environments. HDPE geomembranes are also recognized for their low permeability, about 1×10⁻¹⁴ m/sec, hence ensuring minimal leakage, even in aggressive chemical environments.
However, other materials such as linear low-density polyethylene (LLDPE) and polyvinyl chloride (PVC) are now being introduced into the field for specific purposes. LLDPE, for example, offers increased flexibility and conforms easily to complex subgrades; hence, it is the preferred choice for applications requiring such adaptability. On the other hand, PVC geomembranes are commonly applied where installation and welding ease take precedence, such as lining small reservoirs or decorative ponds.
Such advances in geomembrane technology underpin an industry-wide effort to improve performance while maintaining compatibility with stringent environmental standards. Through continued innovation and robust materials engineering, geomembranes remain foundational elements of effective environmental and structural containment systems.
Applications of Geocomposites
Geocomposites are innovative materials consisting of two or more geosynthetic products combined for enhanced performance in specific applications. Made from various combinations of geotextiles, geomembranes, geogrids, and drainage cores, they are engineered to resolve tough engineering and environmental issues.
Recent developments show a significant adoption of the products to infrastructure works, especially drainage, and filtration. For instance, a recent research found that geocomposites may be able to give a 50% enhancement in drainage efficiency over conventional granular alternatives while achieving 20-30% saving in material costs. Increasingly, these materials are used in landfill capping systems to help in leachate collection and maintain environmental safety.
In addition to this, geocomposites have been proven invaluable in transportation works. They stabilize subgrade during road construction, cutting the maintenance costs by about 25% over the lifetime of the road. Industries utilize geocomposites for erosion control on slopes, where they provide effective soil retention and support vegetation growth.
Their versatility extends to many other sectors, including water management, mining, and energy facilities, underlining their role as a modern approach to geotechnical design. With continued research and development, the prospects of higher performance, sustainability, and cost-effectiveness are ever-extending.
Advances in Liner Technology
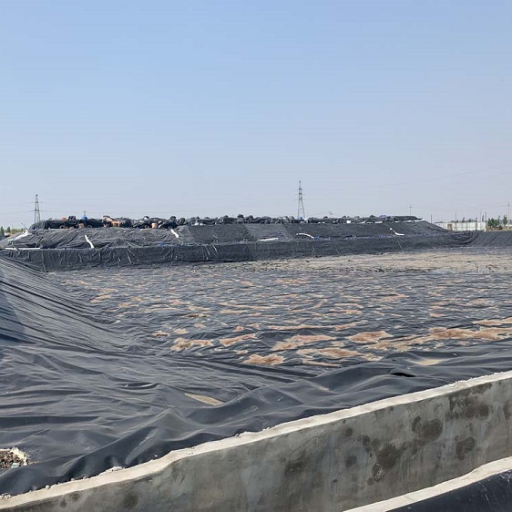
Geosynthetic liner technology has truly undergone novel changes in the last few years, focusing on aspects such as durability, chemical resistance, and environmental performance. The aim of modern liners is to build those barriers which can withstand even harsh working conditions and contain different waste products in landfills and various programs of water conservation. These new developments ensure better performance and high efficacy in reducing environmental harm, conformity to standards, and life expectancy.
Innovations in Material Production
Recent innovations in material production have changed the face of the industry by proposing sustainable and high-performance solutions corresponding to newer specifications. Innovations in polymer science, for instance, have led to the synthesis of biodegradable plastics and super-durable composites. Current data says the global production capacity of bioplastics is anticipated to jump from about 2.9 million tons in 2022 to over 7.5 million tons by 2027, a clear indication of the shift toward greener alternatives.
In addition, breakthroughs have been achieved with nanotechnology, a technique through which one may produce materials with far better strength-to-weight ratios or improved thermal conductivities. The aerospace and automotive companies have embraced such innovations as a means to reduce their energy consumption and increase efficiency. In addition, 3D printing advancements are transforming production capability, facilitating production on demand, and providing customization options, thus significantly minimizing waste.
Such continuous developments within material science reflect the urgent pressure that needs to be put globally on innovation in the direction of balancing performance, cost-effectiveness, and sustainability. Using these technologies, industries will be able to accomplish disruptive innovation whilst concerning the environment and resource efficiency.
Extrusion and the Possible Enhancement of Liner Durability
Extrusion is one of the most important operations for realizing improvements in liner durability and performance necessary in various industrial applications. Through extrusion, raw material is forced into a die with an opening of predetermined shape to create an object of a fixed cross-sectional profile, thus enabling production to occur with consistency and precision in quality. When extrusion is used with liners, such as those used for harsh service in piping systems, automotive components, or chemical containment, it assures uniformity of thickness and a degree of mechanical integrity and wear resistance.
Perhaps the greatest benefit of extrusion with regard to liner production is the ability to work with advanced materials such as HDPE or PVDF. These have the best resistance to corrosion, chemicals, and environmental stress cracking. For instance, studies indicate that HDPE liners manufactured by extrusion methods can present an increase in life span of up to 30% when compared to conventionally manufactured liners, thereby representing a more sustainable and cost-effective solution for mining, water treatment, and oil and gas industries.
Also, through advances in co-extrusion, there is now the option of combining layers of materials with different properties according to function, including chemical resistance, mechanical strength, and thermal stability. This enables liners to be tailored to satisfy performance and durability requirements. For example, studies have shown that co-extruded liners in fuel tanks may reduce permeability rates by as much as 70%, providing safer and more environmentally acceptable systems.
In general extrusion still remains the prime player in conferring improved durability to the liners, with unmatchable precision, material penetration, and long-term utility. With these improvements bearing the great demand for tried and tested industrial solutions, it also aids in reducing waste and promoting sustainability.
Advantages of Geosynthetic Liners Against Traditional Clay Liners
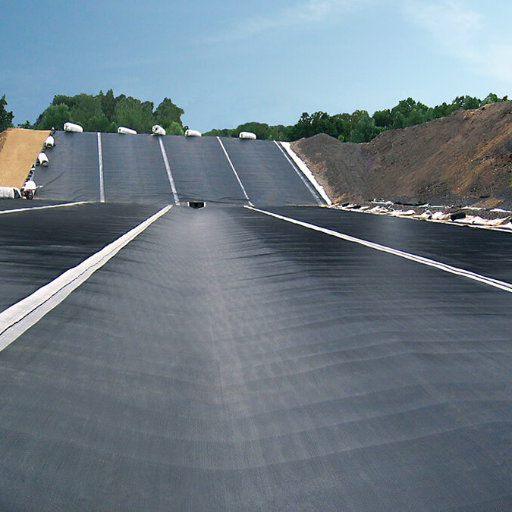
Several advantages are afforded to geosynthetic liners when comparing them to their clay liner counterpart:
Performance: The effectiveness of geosynthetic liners in making spaces impervious is much greater than that of clay liners, preventing the passage of liquids and contaminants.
Durability: They are less likely to snap or crack due to pressure or environmental changes in the lined area.
More Economical: Installation requires lesser time and is less expensive owing to the lesser amounts of material required and a simple installation procedure.
Lightweight: Geosynthetics are easy to transport and handle, allowing free and easy implementation.
Environmental Protection: Liners help reduce groundwater contamination risk.
Simply put, geosynthetic liners present a dependable, efficient, and environmentally friendly solution in the designing of lining systems.
Comparative Study of Performance Indexes
As has been established, geosynthetics exhibit better performance levels compared to traditional lining systems, especially when it comes to durability and cost-efficiency. For instance, studies have shown that with due care and conditions, HDPE (High-Density Polyethylene) geosynthetic liners have the environmental-resistance capability to last more than 100 years, resisting chemical degradation, UV exposures, and mechanical stress.
As one of the landfill case studies has brought to light, geosynthetic liners are able to reduce landfill leakage to less than 1 liter per day per hectare, whereas clay lining systems allow 2,700 liters per day per hectare. This evidently shows that geosynthetics are extremely effective tools of containment. Also, geosynthetic liners can be installed 50% faster than the more conventional ways of installation, translation into even further savings on project schedules and, ultimately, on costs.
Hence, research shows that geosynthetics use 70% less material volume than materials traditionally used for lining, such as compacted clay, and this in itself makes a considerable contribution to a more sustainable and less costly project. This makes geosynthetics a very valuable alternative, not only from the economic point of view but also considering the sustainability of modern life construction and engineering projects.
Cost-Efficiency and Installation Process
Geosynthetics are unmatched by any other material in cost-effectiveness and are lightweight and durable. Recent industry data show that geosynthetics lower construction costs by around 30 percent compared to conventional means because of reduced requirements for material, labor, and installation time. In addition, their installation process requires very few steps and the use of less equipment and machinery, explaining the reduction in the cost of installation; therefore, it helps minimize the environmental footprint of construction projects.
Such type of research evidence sheds light on how, with improved tensile strength and resistance against adverse environmental conditions, modern engineering materials will enhance infrastructure construction. For instance, they have thoroughly now been tested to resist 100 kN/m tensile strength or more, for a myriad of functions ranging from the stabilization of roads to erosion control and landfill lining. According to a recent report, the world geosynthetic markets are expected to reach $22 billion by 2030, with a CAGR of more than 5.5% from 2023, reflecting greater acceptability across numerous construction sectors.
These statistics depict how geosynthetics can benefit project scheduling and cost efficiency while embracing engineering sustainability and efficiency immediate demands of today. Easy installation coupled with excellent long-term performance prospects makes geosynthetics a precious construction material for developing infrastructure of tomorrow.
Environmental Impact and Sustainability
Geosynthetics hugely contribute to reducing an environmental impact on construction projects. Many recent studies substantiate that these materials aid in limiting carbon emissions by solving the presence do with conventional construction means, such as concrete and gravel.
They also promote sustainability practices through improved stabilization and drainage of soils, thus reducing land and degradation erosion. A recent report published by the International Geosynthetics Society states that with geosynthetics, the life of infrastructures is increased by over 40%, thus, reducing the demand for repair and replacement of infrastructure.
Another area of importance is their recyclable nature. Advances have been achieved in polymer technology enabling the production of geosynthetics from recycled materials, thereby promoting circular economy paths. By 2030, the geosynthetics industry is expected to recycle over 2 million tons of polymer waste every year that emphasize that they are, indeed, one of the focal elements in green engineering.
Liner Installation and Construction Practices
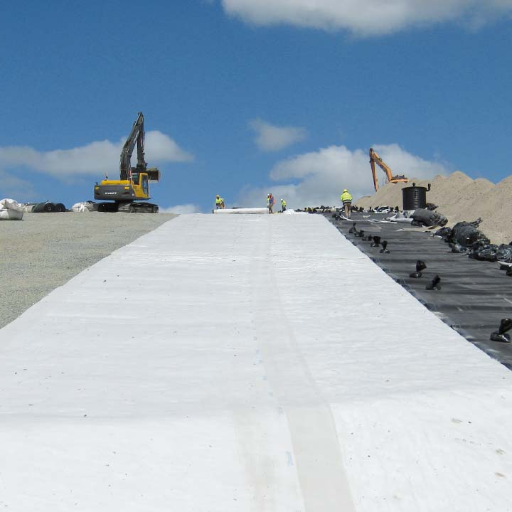
I believe in geosynthetics’ recyclability to foster sustainable engineering practices. If recycled materials are incorporated in their manufacture, polymer waste can be reduced drastically, thereby fulfilling circular economy objectives.
Pre-Installation Assessment of Site and Subgrade Preparation
A proper site assessment and subgrade preparation are paramount for the successful installation and long-term performance of geosynthetics. The assessment commences with an examination of the project site with regard to the soil, hydrological conditions, and possible environmental impact. Identifying these factors at this point enables the engineer to apply solutions for site-specific problems that may compromise the integrity of the geosynthetic materials.
Subgrade preparation is equally important and comprises the clearing, grading, and compacting of the surface where geosynthetics are to be installed. According to the Geosynthetic Institute guidelines, the subgrade must be macro- and microscopically smooth in texture, free from any debris, and compacted to a minimum of 95% of the Standard Proctor Density. Thus, there will be very little chance of either punctures or uneven load distribution, which in turn increases the lifespan of the lined structure.
Subsequently, tests like cone penetration tests (CPT) and moisture content provide critical information on the strength and stability of the soil. For instance, according to researchers, good subgrade preparation can increase the lifespan of a geosynthetic liner by almost 20%, which brings down the repair costs. Also, drainage needs to be catered for so as to avoid water logging, which could cause displacement or failure of geosynthetics. With these preparations in place, the expert can be sure of achieving the highest possible performance along with the sustainability approaches and mandatory regulations.
Detailed Stepwise Procedure of Liner Installation
Site Assessment and Preparation
The first step during liner installation is a thorough site assessment. Soil components, surface water drainage, and surface irregularities are evaluated during this period. The ideal subgrade should be free from sharp objects, debris, and excessive moisture to avoid punctures on the liner or uneven settling.
Data Insight: Recent studies state that a properly prepared subgrade can reduce the possibility of liner failure by 40%, allowing for durability and functionality for a longer time.
Geosynthetic Material Selection
It is imperative to choose the right geosynthetic material for the purpose in hand. HDPE liners, for instance, are most widely used because of their resistance against chemical degradation and UV exposure. Ensure the material adopts international standards such as ASTM D6693 for tensile strength and elongation properties.
Industry Data at Present: The global market for HDPE geomembrane is forecasted to have a CAGR of 6.2% during 2023 to 2030 due to mounting demand in waste management and water containment applications.
Excavation of Anchor Trench
An anchor trench is excavated all-round the liner to securely hold it in place. Such action reduces any risk of shifting or displacement owing to environmental forces, such as wind or water flow.
Liner Deployment
The liners should be installed in calm weather conditions so as not to be damaged by wind or airborne debris. The liner should be carefully unfolded with minimum stretching and tension. Allow sufficient overlap between panels, i.e., 6 to 12 inches, for subsequent welding of seams.
Best Practices Upgraded: Seam welding by hot wedge or extrusion welding will ensure that joints are strong and leak-resistant. Nondestructive testing of the seams by air channel method is recommended to further establish quality.
Inspection and Maintenance
Post-installation inspections will be conducted to ensure any damage, wrinkling, or insufficient seams are repaired. Regular maintenance involving cleaning and wear is key to giving the liner a much longer life.
Research Reports: Failure in inspection maintenance can increase repair costs by about 30%, making preventive maintenance more economically viable over time.
Following these explicit steps and employing the current best practices will assist engineers in optimizing the liner’s performance while cutting down on long-term expenses.
Quality Control and Inspection Practices
Proper quality control and inspection of geosynthetic lining will result in optimal functionality and longevity. Recently, the industry has embraced non-destructive testing (NDT) techniques such as electrical leak detection (ELD) approaches, which engineers may use to pinpoint weaknesses or breaches in liners. Studies show that these technologies can find defects as small as 1 mm, thus reducing the possibility of leaks by 85% compared to mere visual inspections.
Also, for the inspection of liners on a vast scale, thermal imaging by drones is now gathered popularity. This technique gives a quick yet thorough surface analysis in spotlighting areas where uneven distribution of material or improper installation may be a cause for concern. Testimony from the field suggests that thermal imaging can help to halve the inspection time, thus bringing down labour costs without compromising on accuracy.
Another and more futuristic approach to monitoring the condition of liners in real-time supply is developing automated data analytics combined with these inspection tools. Predictive maintenance systems powered by artificial intelligence algorithms can predict failure risks on the basis of historical trends, thereby reducing unplanned downtime by around 30%.
By adopting these innovative processes and technologies, engineers can now make geosynthetic liner systems more trustworthy and cost-efficient, keeping them fully compliant with all environmental and safety standards.
Reference sources
1. Assessment of Municipal Solid-Waste Landfill Liner Performance
- Authors: P. Jain et al.
- Journal: Journal of Environmental Engineering
- Publication Date: September 1, 2023
- Citation Token: (Jain et al., 2023, pp. 1–9)
- Summary:
- This study analyzed leachate collection system (LCS) and leak detection system (LDS) flow rate data from 240 cells across 54 municipal solid-waste landfills with double-liner systems.
- Key Findings:
- The average LCS leachate collection rates ranged from 380 L ha⁻¹ day⁻¹ to 22,400 L ha⁻¹ day⁻¹.
- The average LDS leachate collection rates ranged from 1.8 L ha⁻¹ day⁻¹ to 577 L ha⁻¹ day⁻¹.
- The primary liner systems showed an aggregated efficiency of over 98%.
- Leakage rates were compared with estimates from the HELP model, revealing discrepancies in leakage rate estimations.
2. Geotechnical Properties of Materials Used in Landfill Clay Liner: A Critical Review
- Authors: Rajiv Kumar, Sunita Kumari
- Journal: Sādhanā
- Publication Date: April 11, 2023
- Citation Token: (Kumar & Kumari, 2023, pp. 1–23)
- Summary:
- This review critically examines the geotechnical properties of materials used in landfill clay liners, focusing on their effectiveness in preventing leachate migration.
- Key Findings:
- The study highlights the importance of material selection for landfill liners, emphasizing the need for low permeability and high shear strength.
- It discusses various materials, including natural clays and geosynthetics, and their performance in real-world applications.
3. Utilization of Waste Clay from Boron Production in Bituminous Geosynthetic Barrier (GBR-B) Production as Landfill Liner
- Authors: M. Banar et al.
- Journal: International Journal of Polymer Science
- Publication Date: February 25, 2016
- Citation Token: (Banar et al., 2016, pp. 1–8)
- Summary:
- This study investigates the use of waste clay from boron production as a filler in the production of bituminous geosynthetic barriers for landfill liners.
- Key Findings:
- The study found that the mixture of waste clay and bitumen produced promising results in terms of mechanical behavior and impermeability.
- The research suggests that using waste materials can enhance the sustainability of landfill liner systems.
Frequently Asked Questions (FAQs)
What is a geosynthetic landfill liner and what does it do?
A geosynthetic landfill liner is one of the essential components of new landfill schemes because it is a protective barrier laid down to prevent the migration of leachate and toxic constituents into the surrounding environment. It consists of various layers, including geomembranes and geotextiles, which work in tandem to provide safe containment fulfilling the requirement of secondary containment. These liners prevent the aquifers below from being irreversibly damaged, thus ensuring environmental safety.
In what ways do geotextile materials improve landfill liner performance?
Geotextile materials aid in enhancing the performance of a landfill liner by further filtering, draining, and averting erosion. These are nonwoven or woven fabrics that prevent water from undermining the lining. They may act as a drainage layer, carrying off water flow from above and preventing pressure behind the liner from infringing on stability. Adding layers of geotextile assists engineers in sustaining slope and improving the efficacy of the containment lining in landfill design.
What are the differences between primary and secondary geomembrane liners?
The primary geomembrane liner provides the initial detention for the migration of leachates and is mainly designed to contain waste so as to avoid contamination. The secondary liner provides a back-up containment in case the primary liners leaks. Secondary containment might then consist of a low permeable barriers and leak detection systems that might be employed in the event of a liner contamination procedure.
How does the shear strength of geosynthetics influence landfill stability?
The shear strength of geosynthetics, which include geomembranes and geotextiles, could have direct implications on the stability of landfill cells. With a greater shear strength, the materials withstand the whole force exerted by the waste and maintain the integrity of the liner. By designing landfills considering high shear resistance, liner failure can be minimized and hence leachate migration and groundwater contamination reduced.
What does sodium bentonite do in landfill liners?
Sodium bentonite is used in GCLs due to its relatively low permeability. Upon hydration, sodium bentonite swells up and continues to develop a seal that considerably restricts leachate movement through the liner system. Having such a property makes it a suitable candidate toward achieving better containment capabilities for landfill liners and mitigating associated risk with toxic constituents.
How do erosion control blankets assist in the management of landfills?
Erosion control blankets are used to control surface erosion at landfill sites. These blankets, made of geosynthetics, provide soil stabilization while encouraging vegetation growth, thereby reducing potential sediment runoff. The use of erosion control blankets in landfill management will increase the life span and efficiency of the landfill liners while ensuring the protection of the surrounding environment.
Benefits of using geocomposites in a landfill?
A geocomposite is the combination of two or more geosynthetic materials into one single layer to improve the functioning of landfills. They can act as both drainage layers and protection layers for efficient management of leachate while simultaneously providing structural support. The combination of geosynthetics can greatly speed up installation and reduce costs, thus making their application a majority in modern landfill liner systems.
How would leak detection systems serve as an improvement for the safety of landfill liners?
Leak detection systems are paramount to monitoring the integrity of landfill liners. A detection system equipped with various sensors and monitoring devices can thus identify defects at an early stage, either leakage or failure within the liner materials, giving a chance to be intervened in a timely manner to rectify the problems. Thus enhancement of secured containment of leachate will be ensured as well as the protection of groundwater resource from contamination.