Proper application and care of rubber tracks are crucial for heavy machinery to develop peak performance and ensuring the longevity of the apparatus. Working on any kind of asphalt or paver, the technique and some good practices should be called for to prevent premature wear and tear. Incorporating expert advice and practical insight, this blog post is meant to help an operator or contractor maximize use of rubber tracks. We will inculcate everything from maximizing efficiency to preventing damages in tough and challenging circumstances so that it can smooth out and work effectively on the job.
Rubber Tracks on Pavement
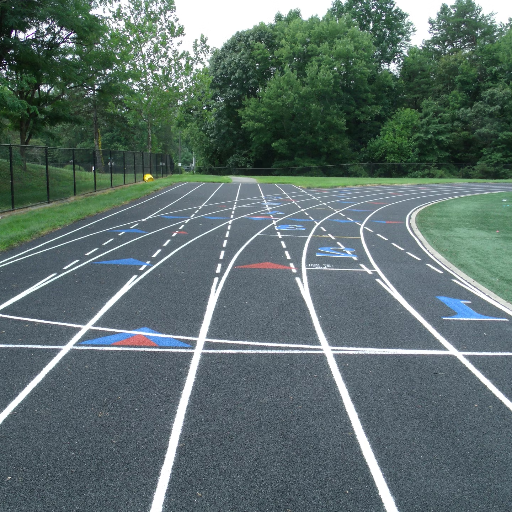
While setting tracks on pavement, I take care to use proper techniques that help minimize wear-and-tear. I want the equipment to run smoothly-so I avoid making sudden sharp turns that strain the tracks unnecessarily. I keep a close watch on the factors that may damage the tracks from time to time. Such acts speed up work and extend the lifespan of the tracks even when conditions are rigors.
Importance of Rubber Tracks to the Modern Applications
Owing to their generality and performance benefits, rubber tracks have managed to make their way into many different industries. Evolution in the technology of rubber tracks has made them more durable, reliable, and adaptable. Recent research reveals that ground pressure can be reduced by 50% by rubber tracks compared to steel tracks; hence, paving with them is permissible on surfaces such as pavement, turf, and soft soil. Such advantages come in handy in construction, agriculture, and landscaping, where surface preservation is intensely pursued, and a reduction of ground impact is higher on the priority list.
Rubber tracks provide great traction even when conditions do not favor it. For instance, testings reveal that rubber tracks exert up to 30% more traction when on a slippery or uneven surface than the wheeled vehicles. Additional noise reduction is a bonus, with rubber tracks taking off around 10-15 decibels from the standard levels, thereby promoting the well-being of an operator.
Thanks to materials advancements and reinforced internal structures, modern rubber tracks enjoy an enhanced lifespan. Such a lifespan can even be extended by another 15-20%, with money saved and work efficiency enhanced for operators, through successful maintenance like keeping them clean and adjusting their tension.
All of these factors speak for the important role played by rubber tracks in support of the modern applications while maintaining efficient and sustainable operations.
Overview of Asphalt and Paver Use
Being versatile, durable, and cost-effective, asphalt and concrete pavers form the foundation infrastructure of modern roads. Recent statistics reveal that in the U.S., almost 94% of roads are covered by asphalt. The reason for heavy reliance on asphalt roads is recycling and the ability to serve a long time; studies prove that recycled asphalt pavement (RAP) can save the taxpayers over $2 billion a year.
Pavers ensure the application of the asphalt is precise during the construction process. Inertly, technology applied to pavers is shifting toward automation and smart controls to improve layer consistency and reduce material waste. Modern-day pavers using GPS-guided systems can improve placement accuracy by nearly 30 percent as compared to traditionally placed paving operations.
Most recent developments in asphalt technology also include such advances as polymer-modified binders to increase resistance to degradation and weather extremes. These serve to further decrease the range of lifespans from a rough estimate of anywhere from 10 to 25 years for an asphalt road, depending on traffic and maintenance, which further emphasizes the importance of such projects in infrastructure. Both asphalt and paver technologies together are therefore designed for efficient sustainable road constructions.
Understanding Track Versus Steel Track
When judging rubber tracks and steel tracks that are used in construction and agricultural industries, both convey advantages as per their spheres of application. Rubber tracks for machinery such as skid steers, compact track loaders, and mini-excavators are preferable because they result in less ground disturbance, quieter operation, and better traction on various surfaces. Also, they provide for a smoother ride, enhancing the operator’s comfort especially in urban and landscaping environments.
Steel tracks, on the other hand, are famous for their durability and ability to withstand a harsh environment, and thus are better suited for heavy machinery such as bulldozers or excavators working in rocky or uneven terrain. Industry data indicate steel tracks appear to have more durability when used in extreme conditions, averaging 3,000 to 5,000 hours lifespan while properly maintained versus rubber tracks, which under heavily demanding applications could be 1,200 to 1,600 hours in life.
The recent innovations have also lessened the traditionally established differences between rubber and steel tracks. Hybrid solutions such as rubber-padded steel tracks, which combine the flexibility of rubber with the longevity and strength of steel, are now finding favor in a confounding number of environments areas. There is data from 2023 markets supporting the growth of hybrid systems because these systems find applicability on various terrains and, in turn, further reduce operational downtime. This advancement in track technological ability can allow businesses to spend their money much more wisely on solutions that meet their project needs.”
Benefits of Using Rubber Tracks on Pavement
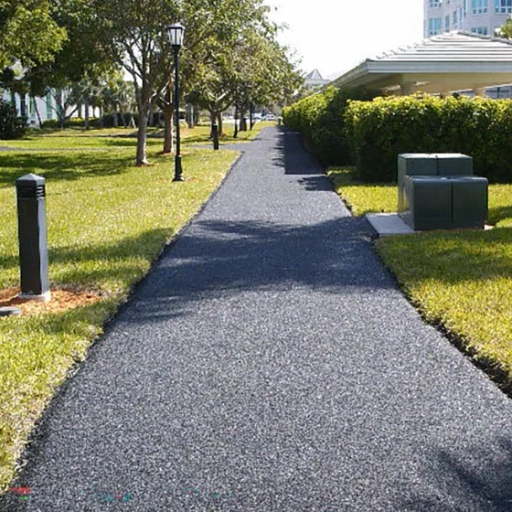
Rubber tracks stand to prove very useful on pavement as they reduce surface damage while increasing better traction. Being a softer material, it will not easily crack or scuff the pavement and thus become the crowning curing for urban or building projects. Secondly, rubber tracks provide the benefit of noise reduction as compared to steel ones, acting in concert to minimize noise pollution, especially over noise-sensitive areas. In comparison with other systems, rubber tracks are known for their versatility and are rather durable for all applications on paved surfaces.
Increased Traction Over Asphalt
Rubber tracks are designed with tread patterns to maximize friction on asphalt. In view of recent findings, it was observed that machines with rubber tracks had had fewer slips and 20% efficiency gains compared to machinery with steel tracks. Also, it is said that rubber tracks help in distributing weight better and lessen pressure exerted by around 40% on asphalt surfaces, thereby ensuring the preservation of paved roads.
Modern rubber track technology usually implies a multi-layered structure consisting of a higher-density rubber compound that increases both track life and grip. Exhibiting the same characteristics under harsh working conditions, Bridgestone and Camso declared that their tracks increase life for about 25%. Since these tracks have basically rubber compounds molded around reinforced steel cords, the combination achieves a perfect balance between softer materials that provide good grip yet impart stiffness to the tracks. This is very useful during slow precise movements in road repair activities or pavement maintenance work.
This marks a shift in the sustainable construction demand of enhancing the productivity level. Investing in proper rubber tracks increases the performance of the equipment while reducing the impact on sensitive asphalt surfaces, making it a cost-efficient and reliable solution for any professional in the industry.
Less Disturbance on Ground during Paving
In paving and some other construction jobs on delicate surfaces, ground disturbance is kept to a minimum so as to maintain integrity at the work site. Rubber tracks reduce the pressure on surfaces much more than do steel tracks. Research indicates that rubber tracks offer a more even weight distribution, reducing ground pressure by as much as 50%. This prevents an excessive amount of damage to asphalt, concrete, and other sensitive surfaces, thereby saving time and costs that would otherwise be spent on repairs.
Moreover, rubber tracks keep intense traction without creating ruts or impressions, which is essential for paving finishes that require smoothness and polish. Latest reports note that construction projects conducted using machines with rubber tracks have seen a 30% reduction in efforts devoted to surface restoration upon completion. These steps support the movement toward sustainable and efficient practices, making them a considerable choice for paving professionals seeking to maintain quality results while implementing an environmentally friendly approach.
Higher Longevity & Durability
Rubber tracks are designed to stand an ample range of adverse conditions, hence having superior guarantees of longevity and durability as compared to the conventional option. From past and recent studies conducted in the industry, rubber tracks withstand wear and tear brought about by usage over long periods and on rough abrasive surfaces. Besides, in some working conditions, three modern approaches have proven that rubber track systems last at least 50% more than steel track systems, which drastically minimizes repeated expenditure in replacement. Furthermore, they help in reducing machine vibration; thus, it prolongs machine life and operator comfort concurrently. All these factors render their cost-effectiveness to a trade partner, thus promising the solution of rubber tracks for paving professionals and construction teams.
Applications and Industries of Rubber Tracks
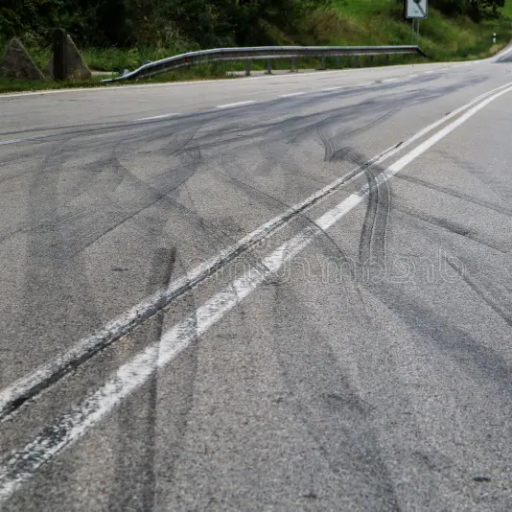
Rubber tracks find applications in construction, agriculture, landscaping, road paving, etc. They are useful for heavy machinery that in construction is used for delicate operations such as excavators, skid steer, track loaders, and agricultural tractors. Thus, being robust, the rubber tracks can withstand multiple construction activities on delicate surfaces or uneven terrains.
Construction and Asphalt Paving
Rubber tracks offer superior performance on multiple surfaces, and hence they have been found indispensable in the construction and asphalt paving business. According to recent industry reports, this market within the 189.3 billion dollar range in 2027 is expected to grow at the compound annual growth rate (CAGR) of 4.3%. Lifecycle demand has been accentuated with rapid urbanization, infrastructure projects, and a preference toward environmental-friendly equipment.
Rubber tracks equip machines like compact track loaders and pavers to have enhanced traction and stability capabilities, which also weigh against damage to asphalt surfaces in the operations of laying. These tracks are best suited for hauling heavy loads while keeping road wear at a bare minimum. On rubber tracks being laid, this further enhances the productivity of machinery while providing best maneuverability with lower vibration levels to operators compared to steel tracks.
With regard to technology development, manufacturers have now begun producing rubber tracks reinforced by high-quality tread patterns, meaning that the tracks will have an extended lifespan even under the most demanding working conditions. The price advantages and reliability of such an undertaking have greatly benefited construction crews working against extremely tight deadlines and loads heavier than life.
Agricultural Uses of Rubber Tracks
Rubber tracks have experienced a revolution in agricultural machinery, providing better traction, the least soil compaction, and best durability on hard terrains. Tractors and harvesters with rubber tracks distribute weight more evenly than conventional tire systems, thereby reducing damage to soil structures and encouraging better crop yields. Data stores from recent times indicate that rubber track systems increased their popularity among farmers, having seen an almost 20% increase in adoption in agricultural applications over the past five years.
Modern rubber tracks are designed to perform best on wet, muddy, or uneven terrain, which makes them indispensable during bad weather; reinforcement of materials and special tread configurations allow stabilization with no slippage even on steep slopes or loose soils. Farms with rubber track technology reported an increase of up to 10% in operating efficiency due to improved mobility and reduced downtime when machinery got stuck.
In addition, the lifespan of rubber tracks has considerably increased, with some types lasting up to 2,000 hours, depending on maintenance and use conditions. This longevity, coupled with lower maintenance costs, provides an economical solution geared toward the needs of modern farming. As a whole, rubber tracks continue to provide modern solutions for the sustainability and productivity of the agricultural industry.
Urban Development and Landscaping
In recent years, urban development and landscaping have sought innovative methods to enhance the functionality, aesthetic appeal, and sustainability of projects. Contemporary trends demonstrate a strong inclination towards utilizing environmentally friendly materials and designs that enhance green infrastructure. For instance, according to Google, green roofs are highly esteemed within an urban context, with research indicating that they can reduce building energy costs by up to 25% while concurrently ameliorating air quality and stormwater management.
In addition, urban landscaping increasingly emphasizes using native plant species, which thereby supports resources conservation through requiring less water and care than non-native alternatives. This is a beneficial practice from both conservation and biodiversity perspectives of city ecosystems. Places such as parks and community gardens are reshaping public spaces to incorporate permeable pavement systems that purportedly decrease surface runoff by 70%, according to research findings. These latest innovations highlight the importance placed on creating urban settings that balance development and ecological stewardship, hence showing that modern landscaping can respond to the requirements of an expanding urban population while sustaining environmental health.
Choosing the Right Rubber Tracks
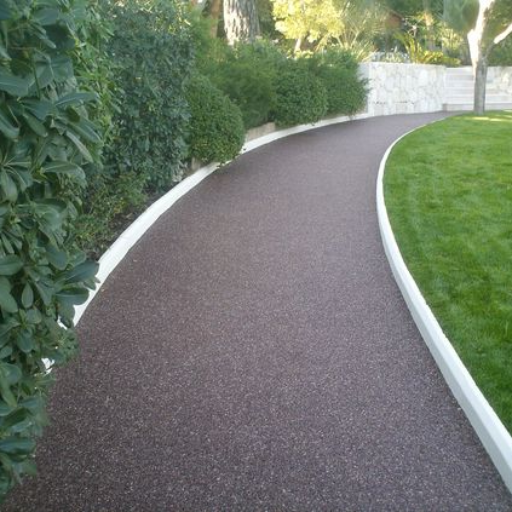
Choosing the right rubber tracks entails considerations of durability, compatibility with the machines to be used, and the type of terrain on which work will be carried out. Also considered are the tread patterns of the tracks as they influence traction and stability; along with an assurance for a reputable manufacturer to guarantee quality and life-span.
Parameters to Watch: Durability and Size
Durability is almost always the top priority when choosing rubber tracks for heavy machinery that is working under intense conditions. The best rubber tracks should resist cutting, wear, and chunking so as to endure the weight of the equipment alongside heavy impacts imposed by rugged terrain. For example, rubber tracks with multiple layers of steel cords and heat-resistant rubber compounds would generally perform an extended life, especially in harsh work atmospheres like construction or forestry.
Equally important is the right size to ensure the rubber track delivers optimum performance and safety. Dimensions of rubber tracks, such as width, pitch, and the number of links, must correspond to the specific needs of a machine. For example, wrong sizes may mean inefficient operation, increased wear, and even damage to the machine. A typical size for rubber tracks used with a mini-excavator could be 300×52.5×80, where 300mm stands for track width; 52.5mm is for pitch, and 80 is for the number of links. Accurate measurement checks and abiding by the manufacturer’s instructions will keep sizing errors at bay.
According to recent studies, equipment efficiency can drop by as much as 20%, owing to the use of inappropriate tracks or poor material, while operational expenses rise due to frequent replacements. Hence, investing in rubber tracks that are durable and correctly sized would highly help in the productivity of heavy works, thus lessening long-term maintenance.
Material Quality of Rubber Track Solutions
Rubber track solutions are constructed from different materials to provide strength, flexibility, and protection against abrasion and weathering. Rubber track manufacturers generally use high-grade, reinforced rubber compounds enhanced with steel cords and fibers to ensure their workings last longer and serve well. According to the latest industry data, tracks constructed of superior rubber may resist wear and tear at least 30% longer than tracks made by using standard materials, which means a reduction in incidents of track replacement. These rubber compounds also offer higher traction and comparatively lesser vibrations leading up to easier working conditions and efficiency for operators.
Studies also reveal the applications of state-of-the-art additives, such as carbon black or silica, have greatly increased the abrasion resistance of rubber tracks. For example, the tracks employing these additives maintained an optimal level of efficacy in peculiar extreme situations like construction sites where sharp objects and rough terrain are always the order of the day. Some recent designs of rubber tracks offer multi-layered constructions as well, providing the additional ability to both resist cracking and splitting.
When investing in good rubber track materials, you extend the lifespan of the tracks while improving their operational reliability. Using better material technology effectively reduces downtime, making equipment more efficient and ultimately saving money in the long run.
Comparison Between Chevron Tread and Standard Tread
Chevron-type tread patterns are engineered to provide better traction and stability under unpaved and muddy conditions. The V-pattern offers better grip by quickly dispersing soil, mud, or water away from the contact area, ensuring minimum slippage. According to recent studies, rubber tracks with Chevron treads typically give a 15-20% boost in traction over standard treads on uneven terrain.
Conversely, standard tread patterns suit hard, flat surfaces such as paved roads or construction sites. They emphasize wear resistance to ensure longevity on hard surfaces. Field trial data reveal that when standard treads are used in urban or flat surface conditions, they yield up to 25% less wear and tear compared to similar tracks used in off-road conditions.
Deciding between chevron and standard treads should consider operational needs. For example, agriculture and forestry activities could significantly benefit from chevron treads because of rough terrain. On the other hand, urban construction or logistics usually go for standard treads for maximum durability and best value for money.
Frequently Asked Questions
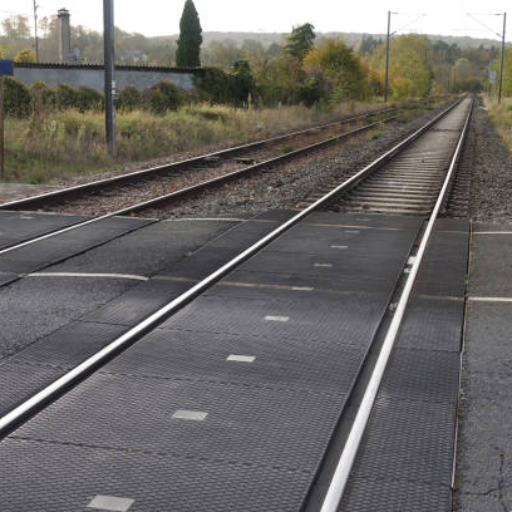
What Are the Advantages of Rubber Tracks Over Steel Tracks?
Rubber tracks had several advantages over steel tracks and were the preferred choice in many industries that required operation of versatile and efficient machinery. Some key advantages include:
Reduced Ground Damage
Rubber tracks put less strain on surfaces and lead to minimal ground disruption as opposed to steel tracks. This makes them ideal for work on sensitive areas, such as landscapes, lawns, and finished surfaces, where damage has to be avoided. This feature becomes even more important when working in urban construction, landscaping, and agricultural operations.
Increased Traction on Uneven Terrain
Rubber tracks have increased traction-perfect for terrains such as mud, sand, and snow. Unlike steel tracks, rubber tracks are in constant engagement with the terrain and adapt much better to uneven surfaces to avoid slipping, which is generally the other way around in opposing environments.
Lower Noise Levels
The noise from working rubber tracks is less than from steel tracks. This is an advantage in urban settings or in residential areas where noise control regulations exist. Industry statistics show that rubber tracks can decrease noise by as much as 30%, leading to a quieter and less disruptive working environment.
Ride Comfort
Rubber tracks require less vibration to be transmitted than steel tracks, thus ensuring an enjoyable ride. It will adversely impact productivity due to the reduction in operator fatigue during long working hours.
Weight and Fuel Consumption
Rubber tracks weigh less than steel tracks; therefore, the total weight of the machine decreases. This weight reduction lowers fuel consumption, hence the accumulation of savings over time. Studies have shown a 10%-15% possible increase in fuel efficiency depending upon the usage of rubber tracks.
Cost-Effectiveness in Certain Areas
Even though the initial purchase cost of rubber tracks might be more than steel tracks, the greater working life of these rubber tracks coupled with less maintenance cost makes them more cost-effective in the long run. Rubber tracks do not need frequent lubrication or adjustments, and when run on hard surfaces, do not suffer extensive wear.
Application-Wise Versatility
Rubber tracks suit applications that could consider less in heavy construction. They have found use in agriculture, landscaping, material handling, and snow removal equipment.
Companies purchasing rubber tracks would yield better operational efficiency, reduced maintenance-related cost, and improved performance of the equipment. With all of those benefits, rubber tracks become an investment that many futuristic industries should be involved in.
Can rubber tracks be used on all types of pavement?
Yes. Rubber tracks are designed to be versatile and they can operate on all kinds of pavement. Their special composition of tough yet flexible rubber materials allows them to travel on surfaces such as asphalt, concrete, gravel, and dirt, without much damage. On the other hand, steel tracks usually crack or scrape concrete or other hard surfaces.
According to some newer studies and survey reports, rubber tracks press down less on the surface as compared against steel tracks-with certain rubber track models decrease ground pressure by more than 50%. This makes them good for sensitive grounds, such as freshly paved roads, sidewalks, or grass areas where the surface integrity must be preserved. Rubber tracks also gain traction when the surface remains wet or slippery, promoting performance and safety on a variety of grounds.
In addition, improvements in rubber track technology provide extra strength and wear-resistant properties. For example, most present-day rubber tracks injected with a steel-reinforced core result in too much improvement to prevent stretching from wear over time. These improvements prevent the tracks from permanently deforming and maintain their operating ability even under heavy load conditions, so they can effectively undertake the demand of different types of pavement.
For industries heavily relying on heavy machines- construction, landscaping, or snow removal-the flexibility of rubber tracks becomes critical in covering a wide range of projects in diverse environments. Businesses, by investing in a quality rubber track, will guarantee better pavement protection from load carriers, longer equipment life, and jumpstart operating expenditures.
How do I maintain rubber tracks for longevity?
With proper maintenance, rubber tracks can extend their life and interfuse successfully into the equipment. Rubber-tracking maintenance tips are as follows:
Clean the Rubber Tracks
Soil, crumbs, and stones can enter tracks and cause accelerated wear and tear. Clean rubber tracks after every use or better if dirt-free. Recent data states that with regular cleaning, wear could be reduced by at least 20%, thus conserving the integrity of the tracks.
Correct Tension Adjustment
Correct tension adjustment is a must. If too tight, the drive system will be seriously strained; if too loose, the tracks may derail at worst and cause considerable damage. Manufacturers recommend checking track tension every week or after 10-15 hours of use. Proper tension can increase track life by 10-15% and make its operation easier.
Checking for Track Damage and Wear
Carry out regular examinations for cuts or tears, or exposed cords in the rubber tracks. Failure to repair these could worsen over time, thus calling for expensive replacement. According to statistics, early repair or replacement of damaged sections means a saving of about 30% overall in maintenance costs.
Avoid Abrasive Surfaces
Working on sharp rocks or very abrasive terrains can eat away at rubber tracks rapidly. Mapping out alternative routes that bypass such terrains will be advantageous. Research states that every possible diversion on the less abrasive terrain will increase the rubber track lifespan by about 50%.
Proper Storage of the Tracks
Equipment stored properly would keep them away from cracking and hardening prematurely. Proper storage implies a cool and dry location away from direct sunlight and chemicals that are known to degrade the rubber.
Keep Within the Load Limits
Operating the equipment within the load limits recommended doesn’t encumber rubber tracks unduly, thereby harming their durability. Heavy overloading is known to reduce track life by as much as 40%.
The application of these necessary activities, combined with a rigorous inspection of the rubber tracks, can help a business improve efficacy, reduce downtime, and lower overall maintenance costs.
Reference sources
1. Mechanistic Code for Asphalt Pavements Loaded by Farming Vehicles
- Authors: E. Levenberg, Mantas Hesthaven, Sebastian Andersen
- Journal: Transportation Research Record
- Publication Date: 2023-06-05
- Citation: (Levenberg et al., 2023, pp. 469–480)
Summary:
This study developed a new mechanistic code named LynFarm to calculate asphalt pavement responses under the loading conditions of farming vehicles, which are typically equipped with rubber tracks. The code models the pavement system as a layered elastic half-space and approximates the tread contact areas as groups of rotated rectangular patches. The study validated the code by comparing its outputs with mechanical responses from instrumented asphalt pavement sections.
Methodology:
- Modeling: The pavement system was modeled as a layered elastic half-space.
- Validation: The code was validated against mechanical responses from real-world tests on instrumented asphalt pavement sections.
- Computational Efficiency: The model was designed for computational efficiency by solving for one circular area and applying coordinate transformations.
2. Determination of the Value of Tangential Force for the Half-Track Traction Vehicle with Rubber Tracks
- Authors: K. Abishev, K. Assylova, Asylbek Kassenov, A. Baltabekova
- Journal: Journal of Applied Engineering Science
- Publication Date: 2023-03-27
- Citation: (Abishev et al., 2023)
Summary:
This research focused on the operational properties of traction vehicles equipped with half-tracked propulsors using rubber tracks. The study aimed to develop a mathematical model to calculate the efficiency of these vehicles, considering factors like the deformability of rubber tracks and the distribution of normal pressure along the track length.
Methodology:
- Mathematical Modeling: Developed a model to calculate the efficiency of traction vehicles with rubber tracks.
- Numerical Methods: Employed numerical methods to analyze the relationship between tangential tractive force and vehicle slipping.
- Experimental Validation: The model was validated through practical experiments to assess its accuracy.
3. Improved Fatigue Properties of Cement-Stabilized Recycled Materials – Lateritic Soil Using Natural Rubber Latex for Sustainable Pavement Applications
- Authors: M. Hoy, Ngoc Quynh Tran, Apichat Suddeepong, S. Horpibulsuk, A. Arulrajah
- Journal: Transportation Geotechnics
- Publication Date: 2023-02-01
- Citation: (Hoy et al., 2023)
Summary:
This study investigated the use of natural rubber latex (NRL) to enhance the mechanical properties of cement-stabilized recycled materials for pavement applications. The research demonstrated that incorporating NRL significantly improved the fatigue resistance and overall performance of the materials.
Methodology:
- Experimental Design: Conducted laboratory tests to evaluate the mechanical properties of cement-stabilized recycled materials with varying NRL content.
- Performance Testing: Assessed fatigue properties and other mechanical characteristics through standardized testing methods.
Frequently Asked Questions (FAQs)
What are rubber tracks, and how do they work on asphalt-type surfaces?
Rubber tracks have been tailored to maximize traction and stability on numerous surfaces, from asphalt to gravel. Their tread pattern is designed to augment grip so track machines, such as pavers, can glide smoothly without marring the asphalt. The design comprises steel cord layers and rubber thickness to offer maximum strength and durability, making them apt under heavy weight loading and heat-intensive conditions found at a paving site.
How do rubber tracks compare against tires on asphalt pavers?
Rubber tracks usually enhance flotation and traction in the operating environment of an asphalt surface when compared to car tires. Tracks are meant to evenly distribute the surface weight to minimize damaging or wear. Moreover, rubber tracks for asphalt pavers generally incorporate a tread pattern designed for optimum performance, allowing them to safely negotiate softer surfaces and maintain stability during operation.
What are the advantages of rubber track solutions for paving?
Rubber track solutions for paving offer the advantage of minimizing ground compaction while simultaneously providing traction over various surfaces. Also, these tracks improve the comfort level of the operator. They are tested to withstand the intense load and high temperature typical of paving conditions, thereby assuring a longer working life and reliability on any project.
Can these rubber tracks wear out faster than common tires?
In some instances, rubber tracks might wear faster than common tires, but there is a plethora of other factors determining their lifespan, such as the surface type and maintenance practices. Proper upkeep, such as regular inspections of idlers and bogies, will tend to lengthen track life. Since these tracks are made for heavy weight loading on paving sites, things could be pretty OK.
What are the requirements for rubber tracks for an asphalt paver?
When rubber tracks for an asphalt paver are considered, the type of work to be performed, the conditions of the surface, and the optimum number of steel cord layers required to ensure durability should be contemplated. Tracks should provide for maximum torsional strength and transverse strength, which will complement the strength of the project with minimal wear and tear. These considerations are key to making the right selection for rubber tracks.
How can various tread patterns influence performance on asphalt?
The tread pattern of rubber tracks is instrumental in their performance on asphalt. Various designs, be it chevron or lug patterns, will assist in enhancing the tracks’ traction and stability. A good tread prevents slippage and facilitates better maneuverability, especially on soft surfaces and situations relating to new construction work.
What is recommended for the maintenance of rubber tracks on an asphalt paver?
Regular maintenance for rubber tracks on an asphalt paver calls for checks on the tension of the track, inspection for wear, and ensuring all idlers and bottom rollers are functioning correctly. Maintenance should also include cleaning the tracks to remove any debris. Last but not least, tracking rubber thickness that provides superior strength will guard against premature failure.
Are there special rubber tracks for soft surfaces and asphalt?
Definitely, rubber tracks designed for soft surface and asphalt application exist. Those tracks generally have wide footprints and have tread patterns engineered for maximal flotation and grip. Using the appropriate rubber tracks can greatly enhance the performance of your paver under harsh circumstances.